77G Radar High Frequency PCB Manufacturer
77G Radar High Frequency PCB Manufacturer,The 77G Radar High Frequency PCB is a specialized printed circuit board engineered for high-performance radar systems operating at the precise microwave frequency of 77 GHz. Designed with advanced materials like PTFE-based laminates, it ensures minimal signal loss and maintains signal integrity crucial for automotive radar applications. With meticulously controlled impedance and transmission line routing, this PCB facilitates reliable detection and distance measurement, vital for adaptive cruise control, collision avoidance systems, and other safety features in vehicles. Its precision fabrication and cutting-edge design make it an indispensable component in modern radar technology, ensuring unparalleled accuracy and efficiency.
What is a 77G Radar High Frequency PCB?
A 77 GHz Radar High Frequency PCB (Printed Circuit Board) is specialized hardware designed for use in radar systems that operate at the high microwave frequency of 77 GHz. This particular frequency band is predominantly used in automotive radar applications, such as adaptive cruise control, collision avoidance systems, and other vehicle safety mechanisms that help in detecting objects and distances in the vehicle’s surroundings.
The design and manufacturing of a 77 GHz High Frequency PCB involve sophisticated technology tailored to handle high-frequency signals with minimal loss and interference. Materials used in these PCBs are typically high-frequency laminates with low dielectric constants and loss tangents, which are essential for maintaining signal integrity at microwave frequencies. Common materials include PTFE (Polytetrafluoroethylene), often reinforced with ceramic fillers, which help in achieving the desired electrical properties and thermal stability.
The layout and trace design of these PCBs are also critical. Due to the high operating frequency, even minor imperfections can lead to significant signal degradation or reflection. Thus, the traces must be precisely engineered to maintain impedance control, minimize insertion loss, and avoid unwanted signal interactions through careful consideration of trace geometry and spacing.
Additionally, these types of PCBs often incorporate advanced features such as embedded passives, microvias, and possibly multiple layers to accommodate the complexity and compactness required by modern radar systems. The use of sophisticated design techniques and specialized manufacturing processes makes the 77 GHz Radar High Frequency PCBs essential yet intricate components in the field of radar technology, especially in applications demanding high precision and reliability.
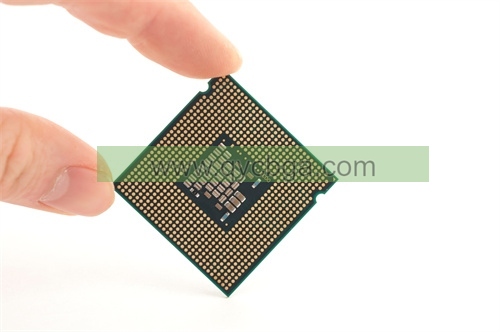
77G Radar High Frequency PCB Manufacturer
What are the 77G Radar High Frequency PCB Design Guidelines?
Designing PCBs for 77 GHz radar applications requires careful attention to various factors to ensure optimal performance. Here are some key design guidelines:
- Material Selection: Choose high-frequency laminates with low dielectric constants (εr) and low loss tangents (tan δ) to minimize signal attenuation and maintain signal integrity. Common materials include PTFE-based substrates like Rogers RO3003 or RO4350B.
- Impedance Control: Maintain consistent impedance throughout the transmission lines to minimize signal reflections and ensure efficient power transfer. Use controlled impedance traces and maintain specified trace widths and separations according to the chosen substrate material.
- Transmission Line Design: Utilize microstrip or grounded coplanar waveguide (GCPW) transmission line configurations for high-frequency signal routing. These configurations offer good impedance control and low loss characteristics.
- Via Design: Minimize the use of vias, especially in high-frequency sections, to reduce signal discontinuities and impedance mismatches. When vias are necessary, use short, stub-less vias with controlled impedance.
- Grounding: Implement a solid ground plane on all layers to provide low impedance return paths for signal currents and minimize electromagnetic interference (EMI). Avoid splitting ground planes beneath high-frequency traces to prevent impedance variations.
- Component Placement: Place critical components, such as mixers, amplifiers, and antennas, close to the radar transceiver to minimize trace lengths and reduce parasitic effects. Maintain appropriate spacing between components to avoid interference.
- Signal Integrity Analysis: Perform electromagnetic simulation and signal integrity analysis using tools like HFSS, CST Microwave Studio, or ADS to verify impedance matching, signal propagation, and electromagnetic compatibility (EMC) compliance.
- Thermal Management: Consider thermal management techniques, such as thermal vias or heat sinks, to dissipate heat generated by high-power components and maintain stable operating temperatures.
- EMC Compliance:Ensure PCB design complies with electromagnetic compatibility (EMC) standards by minimizing emissions and susceptibility to external interference. Shield sensitive components and signal traces, and use appropriate filtering techniques as needed.
- Prototype Testing: Validate PCB designs through prototyping and comprehensive testing, including RF testing, impedance measurements, and thermal analysis, to verify performance and reliability under real-world operating conditions.
By adhering to these design guidelines, engineers can develop PCBs optimized for 77 GHz radar applications, ensuring reliable performance and meeting stringent requirements for high-frequency signal transmission and reception.
What is the 77G Radar High Frequency PCB Fabrication Process?
The fabrication process for 77 GHz Radar High Frequency PCBs involves several specialized steps to ensure high precision and performance at microwave frequencies. Here’s a general overview of the fabrication process:
- Material Selection: Choose high-frequency substrate materials with low dielectric constants and low loss tangents, such as PTFE-based laminates like Rogers RO3003 or RO4350B. Ensure the material meets specifications for dimensional stability, thermal conductivity, and electrical properties.
- Preparation of Substrate: Begin by preparing the substrate material sheets to the required thickness and dimensions. This may involve cutting, cleaning, and surface preparation to ensure proper adhesion of copper foils.
- Copper Cladding: Apply thin copper foils to both sides of the substrate material using a lamination process. The copper foil thickness should match the design requirements for signal traces and ground planes.
- Etching: Use photolithography techniques to create a patterned resist layer on the copper foils, defining the desired circuit traces, pads, and vias. Then, etch away the unwanted copper using chemical or plasma etching processes, leaving behind the desired conductive patterns.
- Drilling: Drill holes for vias and component mounting pads using precision drilling equipment. For high-frequency PCBs, utilize laser drilling or mechanical drilling with controlled depth to ensure accurate hole dimensions and minimal damage to the substrate.
- Plating: Electroplate the drilled holes with conductive materials such as copper or silver to create vias and through-hole connections, ensuring low impedance paths between layers.
- Surface Finish: Apply a surface finish to protect exposed copper surfaces from oxidation and facilitate soldering during assembly. Common surface finishes for high-frequency PCBs include immersion gold, immersion silver, or electroless nickel immersion gold (ENIG).
- Silkscreen and Legend Printing: Optionally, apply silkscreen printing and legend marking to indicate component placement, polarity, and other relevant information on the PCB surface.
- Quality Assurance: Conduct thorough quality control inspections and tests throughout the fabrication process to verify dimensional accuracy, impedance matching, signal integrity, and adherence to design specifications.
- Final Inspection and Packaging: Inspect the finished PCBs for any defects or irregularities before packaging and shipping. Ensure proper handling and protection during transportation to prevent damage to the delicate high-frequency circuits.
By following these steps and employing advanced manufacturing techniques, engineers can produce high-quality 77 GHz Radar High Frequency PCBs optimized for reliable performance in demanding radar applications.
How Do You Manufacture a 77G Radar High Frequency PCB?
Manufacturing a 77 GHz Radar High Frequency PCB involves a series of specialized processes to ensure precise fabrication and optimal performance at microwave frequencies. Here’s a step-by-step guide to manufacturing such a PCB:
- Design Preparation: Begin with the PCB design files generated using CAD software. Ensure the design complies with specifications for 77 GHz radar applications, including impedance control, transmission line routing, and component placement.
- Material Selection: Choose high-frequency substrate materials with low dielectric constants and low loss tangents, such as PTFE-based laminates like Rogers RO3003 or RO4350B. Order the substrate material sheets to the required thickness and dimensions.
- Preparation of Substrate: Clean the substrate material sheets to remove any contaminants and ensure proper adhesion of copper foils. Cut the sheets to the desired dimensions using precision cutting equipment.
- Copper Cladding: Laminate thin copper foils to both sides of the substrate material using a heated press or vacuum lamination process. Control the lamination process parameters to achieve consistent copper thickness and optimal adhesion to the substrate.
- Photoresist Application: Apply a layer of photoresist material to the copper-clad substrate surfaces using a roller or spray coating method. Ensure uniform coverage and thickness of the photoresist layer.
- Exposure and Development: Transfer the PCB design pattern onto the photoresist layer using photolithography techniques. Expose the photoresist layer to UV light through a photomask containing the desired circuit pattern. Develop the exposed photoresist to remove the unexposed areas, revealing the copper traces pattern.
- Etching: Etch away the exposed copper traces using chemical or plasma etching processes. Monitor the etching process carefully to achieve precise trace widths and maintain uniform etch rates across the PCB surface.
- Drilling: Drill holes for vias and component mounting pads using precision drilling equipment. Utilize laser drilling or mechanical drilling with controlled depth to ensure accurate hole dimensions and minimal substrate damage.
- Plating: Electroplate the drilled holes with conductive materials such as copper or silver to create vias and through-hole connections. Control the plating process parameters to achieve uniform plating thickness and good adhesion to the substrate.
- Surface Finish: Apply a surface finish to protect exposed copper surfaces from oxidation and facilitate soldering during assembly. Common surface finishes for high-frequency PCBs include immersion gold, immersion silver, or electroless nickel immersion gold (ENIG).
- Silkscreen and Legend Printing: Optionally, apply silkscreen printing and legend marking to indicate component placement, polarity, and other relevant information on the PCB surface.
- Quality Assurance: Conduct thorough quality control inspections and tests throughout the manufacturing process to verify dimensional accuracy, impedance matching, signal integrity, and adherence to design specifications.
- Final Inspection and Packaging: Inspect the finished PCBs for any defects or irregularities before packaging and shipping. Ensure proper handling and protection during transportation to prevent damage to the delicate high-frequency circuits.
By following these manufacturing steps and employing advanced fabrication techniques, manufacturers can produce high-quality 77 GHz Radar High Frequency PCBs optimized for reliable performance in demanding radar applications.
How Much Should a 77G Radar High Frequency PCB Cost?
The cost of a 77 GHz Radar High Frequency PCB can vary significantly depending on several factors, including the complexity of the design, the quality of materials used, the manufacturing process, and the quantity ordered. Here are some key factors that can influence the cost:
- Design Complexity: PCBs with intricate layouts, high layer counts, tight tolerances, and advanced features such as embedded passives or controlled impedance traces will generally cost more to manufacture.
- Material Selection: High-frequency laminates with low dielectric constants and low loss tangents, such as PTFE-based substrates, tend to be more expensive than standard FR-4 materials.
- Manufacturing Process: Advanced fabrication techniques, such as laser drilling, controlled impedance routing, and surface finish options like immersion gold, can add to the manufacturing cost.
- Quantity: Larger production runs typically result in lower per-unit costs due to economies of scale. Ordering higher quantities can reduce the cost per PCB.
- Additional Services: Additional services such as assembly, testing, and inspection may incur extra charges.
- Supplier Selection: Different PCB manufacturers may offer varying pricing structures and capabilities. Factors such as reputation, quality standards, and lead times can also impact the overall cost.
As a rough estimate, the cost of a 77 GHz Radar High Frequency PCB can range from tens to hundreds of dollars per unit for small to medium quantities. For large-scale production or custom designs with complex requirements, the cost per unit may decrease accordingly.
It’s essential to obtain quotes from multiple PCB manufacturers and carefully evaluate the pricing, capabilities, and quality of service offered to find the best balance between cost and performance for your specific application.
What is 77G Radar High Frequency PCB Base Material?
The base material used for 77 GHz Radar High Frequency PCBs is typically selected for its electrical properties, thermal stability, and suitability for high-frequency applications. One commonly used material is PTFE (Polytetrafluoroethylene), which offers excellent electrical insulation properties, low dielectric loss, and stable dielectric constant over a wide range of frequencies.
Within the category of PTFE-based substrates, there are various options available, including:
- Rogers RO3003:A high-frequency laminate with a low dielectric constant (εr ≈ 3.0) and low loss tangent, suitable for applications requiring excellent signal integrity at frequencies up to 77 GHz.
- Rogers RO4350B: Another PTFE-based laminate known for its low dielectric constant (εr ≈ 3.48) and consistent electrical performance over a broad frequency range, making it suitable for high-frequency designs.
These materials provide the necessary electrical characteristics to maintain signal integrity and minimize signal loss at microwave frequencies. Additionally, they offer good thermal stability, mechanical strength, and compatibility with standard PCB fabrication processes, making them ideal choices for 77 GHz Radar High Frequency PCBs.
It’s important to select a base material that meets the specific requirements of the radar system, considering factors such as impedance control, signal attenuation, and thermal management to ensure reliable performance in high-frequency applications.
Which Company Makes 77G Radar High Frequency PCB?
Manufacturing 77G radar high-frequency PCBs is typically carried out by specialized PCB manufacturing companies. Some well-known PCB manufacturers, such as Rogers Corporation, Isola Group, Taconic Advanced Dielectric Division, etc., offer customized high-frequency PCB services to meet the requirements of 77 GHz radar applications.
Our company is also a professional PCB manufacturer with advanced production equipment and an experienced technical team. We can produce 77G radar high-frequency PCBs that meet your requirements. Here are the capabilities and advantages of our company in producing 77G radar high-frequency PCBs:
- Professional Team: We have an experienced team of engineers familiar with high-frequency circuit design and manufacturing technology, able to provide customized solutions for you.
- Advanced Equipment: We use the most advanced PCB production equipment and processes to ensure the production of high-quality PCB products.
- Strict Quality Control: We implement a rigorous quality management system, monitoring every step from raw material procurement to production to ensure that products meet customer requirements and industry standards.
- Flexible Production: We can flexibly handle orders of different scales and complexities, providing production services ranging from small to large quantities according to customer needs.
- Timely Delivery: We are committed to delivering customer orders on time, ensuring the smooth progress of customer projects.
By choosing our company as your PCB manufacturing partner, you can get high-quality, customized 77G radar high-frequency PCBs and enjoy the convenience and trust brought by our professional team and quality service.
What Are the 7 Qualities of Good Customer Service?
Good customer service is essential for maintaining customer satisfaction and loyalty. Here are seven qualities that characterize excellent customer service:
- Responsiveness:Good customer service involves promptly addressing customer inquiries, concerns, and requests. Responding to customer needs in a timely manner demonstrates attentiveness and a commitment to customer satisfaction.
- Empathy: Empathy is the ability to understand and share the feelings of others. Effective customer service representatives show empathy by listening attentively to customers, acknowledging their concerns, and demonstrating understanding and compassion.
- Clear Communication: Clear and effective communication is crucial for providing good customer service. Customer service representatives should communicate information clearly, using language that is easy to understand and free from ambiguity.
- Problem-solving Skills: Good customer service involves resolving customer issues and concerns effectively. Customer service representatives should possess strong problem-solving skills, enabling them to identify root causes of problems and implement appropriate solutions to meet customer needs.
- Professionalism: Professionalism encompasses various attributes such as courtesy, politeness, and respectfulness. Customer service representatives should maintain a professional demeanor at all times, treating customers with courtesy and respect, regardless of the situation.
- Product Knowledge:Customer service representatives should have a comprehensive understanding of the products or services offered by the company. This enables them to answer customer questions accurately, provide relevant information, and offer appropriate recommendations or solutions.
- Follow-up and Feedback: Following up with customers after resolving an issue or completing a transaction demonstrates a commitment to customer satisfaction. Additionally, seeking feedback from customers about their experiences allows companies to identify areas for improvement and make necessary adjustments to enhance the quality of customer service.
By embodying these qualities, companies can deliver exceptional customer service experiences that build trust, foster loyalty, and drive customer retention.
FAQs
What is a 77G Radar High Frequency PCB?
A 77G Radar High Frequency PCB is a specialized printed circuit board designed for use in radar systems operating at the high microwave frequency of 77 GHz. These PCBs are crucial components in automotive radar applications, such as adaptive cruise control and collision avoidance systems.
What are the key features of 77G Radar High Frequency PCBs?
High-frequency laminates with low dielectric constants and low loss tangents, precise impedance control, controlled transmission line routing, and advanced fabrication techniques are key features of 77G Radar High Frequency PCBs. These features ensure optimal signal integrity and performance at microwave frequencies.
What materials are used in manufacturing 77G Radar High Frequency PCBs?
Common materials used in manufacturing 77G Radar High Frequency PCBs include PTFE-based laminates like Rogers RO3003 or RO4350B. These materials offer low dielectric constants, low loss tangents, and stable electrical properties suitable for high-frequency applications.
What are the design guidelines for 77G Radar High Frequency PCBs?
Design guidelines for 77G Radar High Frequency PCBs include maintaining impedance control, utilizing microstrip or grounded coplanar waveguide transmission lines, minimizing signal reflections, and incorporating advanced features like embedded passives and thermal management techniques.
What is the fabrication process for 77G Radar High Frequency PCBs?
The fabrication process for 77G Radar High Frequency PCBs involves steps such as material preparation, copper cladding, photoresist application, etching, drilling, plating, surface finish application, and quality assurance testing. Advanced techniques like photolithography and laser drilling may be used to achieve precision at high frequencies.
What factors affect the cost of 77G Radar High Frequency PCBs?
The cost of 77G Radar High Frequency PCBs depends on factors such as design complexity, material selection, manufacturing process, quantity ordered, additional services required, and supplier selection. Higher complexity and lower quantities tend to increase costs.
Which companies manufacture 77G Radar High Frequency PCBs?
Several PCB manufacturers, including Rogers Corporation, Isola Group, and Taconic Advanced Dielectric Division, offer customized high-frequency PCB services suitable for 77G radar applications. Additionally, specialized PCB manufacturers may provide tailored solutions for specific requirements.