Megtron6 Materials PCB Manufacturer
Megtron6 Materials PCB Manufacturer,Megtron6 Materials PCB is a high-performance printed circuit board material designed for high-frequency and high-speed data transmission applications. This material utilizes low dielectric loss glass fiber substrate and offers excellent thermal stability and mechanical strength. Megtron6 PCBs exhibit outstanding signal integrity and electrical performance, supporting complex design requirements including controlled impedance, reduced signal distortion, and cross-talk. They are widely used in high-speed communication equipment, computer servers, high-performance computing systems, and automotive electronics, providing a reliable foundation and stability assurance for modern electronic devices.
What is a Megtron6 Materials PCB?
Megtron 6 is a type of high-performance PCB (Printed Circuit Board) material known for its advanced electrical properties and reliability. It belongs to the family of advanced laminate materials designed to meet the demanding requirements of high-speed digital applications, such as telecommunications, computing, and aerospace industries.
Megtron 6 PCBs are characterized by their excellent signal transmission capabilities at high frequencies, low transmission loss, and stable dielectric constant over a wide frequency range. These properties make them suitable for designs where maintaining signal integrity and minimizing electrical losses are critical.
In addition to its electrical performance, Megtron 6 offers good thermal stability, which is important for maintaining the structural integrity of the PCB under varying temperature conditions. This feature contributes to the overall reliability and longevity of electronic devices using Megtron 6 PCBs.
Manufacturers often choose Megtron 6 for applications requiring high data transfer rates, such as in high-speed digital designs and RF (Radio Frequency) applications. Its ability to support increasingly complex circuit designs while maintaining high signal fidelity makes it a preferred choice in modern electronics manufacturing.
Overall, Megtron 6 PCB materials represent a significant advancement in PCB technology, addressing the needs of industries where performance, reliability, and signal integrity are paramount.
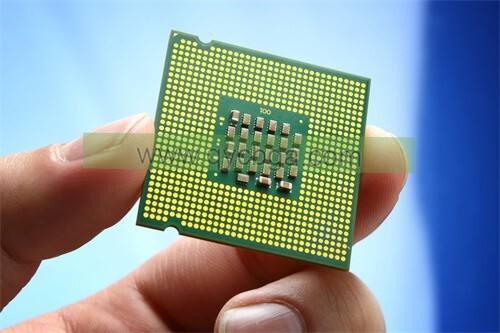
Megtron6 Materials PCB Manufacturer
What are the Megtron6 Materials PCB Design Guidelines?
Designing PCBs using Megtron 6 materials requires adherence to specific guidelines to optimize performance and ensure reliability. Here are some key design guidelines for Megtron 6 PCBs:
- Impedance Control:Megtron 6 has a stable and predictable dielectric constant over a wide frequency range. Designers should calculate and control trace widths, spacing, and layer stackups to maintain desired impedance values. This is critical for high-speed digital signals and RF circuits.
- Layer Stackup:Optimal layer stackup design is crucial for signal integrity and thermal management. Megtron 6 PCBs typically use multiple layers to achieve desired electrical performance. Designers should consider factors like signal layers, power planes, and ground planes to minimize noise and interference.
- Via Design:Proper via design is essential for maintaining signal integrity and thermal management. Designers should use appropriate via types (e.g., microvias for high-density designs) and ensure sufficient via structures to minimize impedance discontinuities.
- Thermal Management:Megtron 6 offers good thermal stability, but effective heat dissipation is still important, especially in high-power applications. Designers should incorporate thermal vias, thermal pads, and possibly heatsinks to manage heat effectively.
- Material Properties:Understand and utilize the specific electrical and mechanical properties of Megtron 6. These include its low dissipation factor (Df) and excellent thermal reliability, which contribute to overall performance and longevity of the PCB.
- Manufacturing Considerations: Megtron 6 PCBs may require specialized manufacturing techniques due to their high-performance nature. Ensure that the chosen PCB manufacturer is capable of handling the material and meeting design specifications.
- Signal Integrity Analysis:Conduct thorough signal integrity simulations and analysis to verify that the design meets electrical performance requirements. This includes checking for reflections, crosstalk, and signal attenuation.
- Design for Manufacturing (DFM):Follow DFM guidelines to ensure the design is manufacturable with Megtron 6 materials. Consider factors like minimum trace width/spacing, via pad sizes, and assembly requirements.
By following these guidelines, designers can leverage the high-performance characteristics of Megtron 6 materials to create reliable and efficient PCB designs for demanding applications in telecommunications, computing, aerospace, and other industries requiring high-speed and high-frequency performance.
What is the Megtron6 Materials PCB Fabrication Process?
Fabricating PCBs using Megtron 6 materials involves several steps to ensure the material’s high-performance characteristics are maintained throughout the manufacturing process. Here’s an overview of the typical fabrication process for Megtron 6 PCBs:
- Material Selection:Choose Megtron 6 laminate material based on the specific requirements of the PCB design, such as high-speed digital signals or RF applications. Megtron 6 materials are selected for their stable electrical properties, low dissipation factor (Df), and thermal stability.
- Preparation of Substrates:The first step involves preparing the laminate materials. This includes cutting the Megtron 6 sheets to the required sizes for the PCB layers. Each layer may undergo surface treatment processes to enhance adhesion during lamination.
- Layer Stackup Design:Design the PCB layer stackup based on the specific requirements of the circuit design. Megtron 6 PCBs often have multiple layers to accommodate complex circuits and ensure signal integrity. Designers consider factors like signal layers, power planes, and ground planes to optimize electrical performance.
- Circuit Pattern Imaging (Lithography):The next step is to create the circuit pattern on each layer of the PCB. This is typically done using photolithography, where a photoresist is applied to the substrate, exposed to UV light through a mask, developed to remove excess resist, and then etched to create the desired circuit pattern.
- Drilling:Drill holes for vias and component mounting pads. Megtron 6 PCBs may use microvias for high-density interconnects, requiring precise drilling capabilities. After drilling, the holes are cleaned to remove debris and ensure proper plating adhesion.
- Via Formation:Create the necessary vias to connect different layers of the PCB. For Megtron 6, this may involve sequential lamination with appropriate via fill materials to maintain electrical integrity and reliability.
- Lamination:Laminate all layers together using heat and pressure. This process bonds the layers into a single structure, ensuring electrical continuity and mechanical strength. The lamination process must be carefully controlled to prevent delamination and ensure uniform material properties across the PCB.
- Plating and Surface Finish:Plate the PCB surfaces with copper to create conductive traces and pads. Apply a surface finish to protect the copper traces from oxidation and facilitate soldering during assembly. Common surface finishes for Megtron 6 PCBs include ENIG (Electroless Nickel Immersion Gold), OSP (Organic Solderability Preservatives), or HASL (Hot Air Solder Leveling).
- Etching and Stripping:Remove excess copper and resist materials through etching and stripping processes to reveal the final circuit traces and pads.
- Testing and Inspection:Perform electrical tests to ensure the PCB meets design specifications for impedance, continuity, and signal integrity. Inspect the PCB for defects such as shorts, opens, or manufacturing flaws.
- Final Finishing:Cut the PCB into individual boards, apply silkscreen legend for component labeling, and perform any final surface cleaning or protective coating as needed.
- Assembly:Once fabricated, Megtron 6 PCBs are ready for component assembly using standard SMT (Surface Mount Technology) or through-hole assembly techniques.
Throughout the fabrication process, strict quality control measures are implemented to ensure Megtron 6 PCBs meet performance standards and reliability requirements for their intended applications, such as high-speed digital communication and RF circuits. Advanced manufacturing equipment and processes are often employed to handle the unique properties of Megtron 6 materials effectively.
How do you manufacture a Megtron6 Materials PCB?
Manufacturing a PCB using Megtron 6 materials involves a series of precise steps to harness its high-performance characteristics, ensuring reliability and optimal electrical properties. Here’s an expanded explanation of the manufacturing process for Megtron 6 PCBs:
- Material Selection and Preparation:Select Megtron 6 laminate material based on the specific requirements of the PCB design, such as high-frequency signal integrity or thermal stability. Megtron 6 is chosen for its low dissipation factor (Df), stable dielectric constant over a wide frequency range, and excellent thermal reliability. Prepare the laminate sheets by cutting them to size according to the PCB design specifications.
- Layer Stackup Design:Design the PCB layer stackup considering factors like signal layers, power planes, and ground planes. Megtron 6 PCBs typically utilize multiple layers to accommodate complex circuits and ensure proper signal integrity. The layer stackup design is crucial for managing impedance control and minimizing signal loss at high frequencies.
- Circuit Pattern Imaging (Lithography):Start by applying a layer of photoresist onto the Megtron 6 substrate. Use photolithography techniques where UV light is passed through a photomask onto the photoresist, exposing the desired circuit pattern. After exposure, develop the photoresist to remove unexposed areas, leaving behind the circuit pattern. The substrate is then etched to remove copper from the areas not protected by the developed photoresist, forming the conductive traces and pads.
- Drilling:Drill holes for vias and component mounting pads. Megtron 6 PCBs may require precision drilling, especially for microvias used in high-density interconnects. After drilling, clean the holes thoroughly to remove any debris and ensure good adhesion during subsequent processes.
- Via Formation:Create vias to establish electrical connections between different layers of the PCB. Depending on the design, this may involve through-hole plating (PTH) or the use of microvias for finer pitch and increased routing density. Fill vias with conductive material, such as copper plating, to maintain electrical continuity and ensure mechanical strength.
- Lamination:Laminate all prepared layers together under heat and pressure. This process bonds the layers into a single, unified structure. For Megtron 6 PCBs, the lamination process must be carefully controlled to prevent delamination and ensure uniform material properties throughout the PCB. The lamination step is critical for maintaining the PCB’s electrical performance and mechanical integrity.
- Plating and Surface Finish:Plate the exposed copper surfaces with additional copper to form the conductive traces and pads on the PCB. Apply a surface finish to protect the copper and facilitate soldering during assembly. Common surface finishes for Megtron 6 PCBs include Electroless Nickel Immersion Gold (ENIG), Organic Solderability Preservatives (OSP), or Hot Air Solder Leveling (HASL). The choice of surface finish depends on factors like environmental conditions, solderability requirements, and component assembly methods.
- Etching and Stripping:Remove excess copper and any remaining photoresist from the PCB using etching and stripping processes. Etching selectively removes unwanted copper while leaving the circuit traces intact. Stripping removes the remaining photoresist and etching residues from the PCB surface to prepare it for subsequent manufacturing steps.
- Testing and Inspection:Perform comprehensive electrical tests and inspections to ensure the PCB meets design specifications and quality standards. Electrical testing verifies parameters such as impedance, continuity, and signal integrity. Visual inspections check for defects such as shorts, opens, or manufacturing flaws that could affect PCB functionality.
- Final Finishing and Assembly:Complete final finishing processes such as cutting the PCB into individual boards, applying silkscreen legend for component labeling, and performing any additional surface cleaning or protective coating as necessary. Megtron 6 PCBs are then ready for component assembly using standard SMT (Surface Mount Technology) or through-hole assembly techniques, depending on the design requirements and application.
Throughout the entire manufacturing process, from material selection to final assembly, stringent quality control measures are implemented to ensure Megtron 6 PCBs meet the high-performance standards required for applications in telecommunications, computing, aerospace, and other demanding industries.Advanced manufacturing equipment and expertise are essential to handle the unique properties of Megtron 6 materials effectively and consistently produce reliable PCBs that meet stringent performance criteria.
How much should a Megtron6 Materials PCB cost?
The cost of a Megtron 6 PCB can vary significantly based on several factors, including the size and complexity of the PCB, the number of layers, the quantity ordered, and the specific requirements of the design and manufacturing process. Here are some considerations that influence the cost:
- Material Cost:Megtron 6 is a high-performance material known for its excellent electrical properties and reliability. It typically commands a higher price compared to standard FR-4 or other laminate materials due to its advanced characteristics. The cost of Megtron 6 laminate per square meter will impact the overall PCB cost.
- Layer Count:PCBs made with Megtron 6 often have multiple layers to accommodate complex circuit designs. The number of layers affects manufacturing complexity and cost, as each additional layer increases material usage and fabrication time.
- Board Size and Shape:Larger PCBs require more material and may involve higher manufacturing costs due to increased processing time and handling. Unusual shapes or cutouts may also impact costs depending on the manufacturing techniques required.
- Trace Density and Complexity:High-density PCB designs with fine-pitch components, microvias, and tight trace routing contribute to higher manufacturing costs. These designs require precision manufacturing processes and may involve additional steps such as laser drilling for microvias.
- Surface Finish and Special Requirements: The choice of surface finish (e.g., ENIG, OSP, HASL) and any additional special requirements (e.g., impedance control, special tolerances) can affect the cost. Certain surface finishes or additional processes may incur extra charges.
- Quantity Ordered:Larger production runs typically reduce the per-unit cost due to economies of scale. However, prototype or small-batch orders may have higher costs per unit due to setup and handling fees.
- Lead Time and Manufacturing Location:Urgency in production or choosing a manufacturer in a specific region can influence costs. Expedited manufacturing or sourcing from regions with varying labor and overhead costs can impact overall pricing.
Given these factors, the cost of a Megtron 6 PCB can range broadly. As a rough estimate, for standard 4-layer Megtron 6 PCBs with typical dimensions and standard specifications, prices might start around $50-$100 per board for small quantities. However, costs can increase significantly for larger, more complex designs with specialized features and requirements.
For accurate pricing, it’s essential to consult with PCB manufacturers or suppliers who can provide detailed quotes based on your specific design specifications, quantity requirements, and desired lead times. Additionally, discussing design optimizations and material alternatives with manufacturers can help balance cost considerations without compromising performance or reliability.
What is Megtron6 Materials PCB base material?
Megtron 6 is a type of high-performance PCB (Printed Circuit Board) base material manufactured by Panasonic. It falls under the category of advanced laminate materials specifically designed to meet the demanding requirements of high-speed digital and RF (Radio Frequency) applications.
The base material of Megtron 6 PCBs consists of several key components and features:
- Resin System:Megtron 6 uses a high-performance resin system that provides excellent thermal stability, low dissipation factor (Df), and a stable dielectric constant over a wide frequency range. This resin system is crucial for maintaining signal integrity and minimizing electrical losses in high-frequency applications.
- Glass Cloth:Megtron 6 laminates typically incorporate glass cloth as a reinforcement material. The choice of glass cloth and its weave style can impact the PCB’s mechanical strength, thermal properties, and dimensional stability.
- Copper Foil: Copper foil layers are embedded within the Megtron 6 laminate material. Copper is essential for forming conductive traces, pads, and ground planes on the PCB surface. The thickness and quality of copper foil affect the PCB’s electrical conductivity and current-carrying capacity.
- Additives and Fillers:To enhance specific properties such as thermal conductivity, dimensional stability, and chemical resistance, Megtron 6 may include additives and fillers. These materials are carefully selected to optimize the overall performance of the PCB in various operating conditions.
- Surface Treatment:Surface treatment processes may be applied to Megtron 6 materials to improve adhesion during PCB fabrication processes such as lamination, drilling, and plating.
Megtron 6 materials are known for their advanced electrical characteristics, including low insertion loss, high thermal reliability, and excellent signal transmission capabilities. These properties make Megtron 6 PCBs suitable for applications where maintaining signal integrity, minimizing noise, and ensuring reliability under harsh environmental conditions are critical.
Manufacturers and designers choose Megtron 6 PCB base materials for their ability to support high-speed digital designs, RF circuits, and other applications requiring robust performance and consistent electrical properties across a range of frequencies.
Which company makes Megtron6 Materials PCBs?
Megtron 6 PCB materials are manufactured by Panasonic Corporation. Panasonic is a globally renowned electronics manufacturer, and its electronic materials division specializes in developing and producing high-performance PCB materials, including the Megtron series. Megtron 6 PCB materials are well-known for their excellent electrical characteristics and stability, particularly suitable for high-speed digital signals and RF applications.
Our company is capable of producing Megtron 6 PCBs, equipped with advanced production equipment and extensive manufacturing experience. Here’s how we manufacture Megtron 6 PCB materials:
- Material Selection and Procurement:We collaborate with reliable suppliers to ensure the procurement of high-quality Megtron 6 laminate materials. These materials possess stable dielectric constants, low dissipation factors, and excellent thermal stability, making them suitable for complex circuit designs and high-frequency applications.
- Design and Engineering Support:Our experienced engineering team provides comprehensive support, from PCB design optimization to manufacturing feasibility analysis. We customize the layer stackup design of Megtron 6 PCBs according to customer requirements, ensuring optimal signal integrity and electrical performance.
- Manufacturing Process Control:We employ advanced manufacturing processes and stringent quality control measures to ensure that each batch of Megtron 6 PCBs meets design specifications and customer requirements. From material preparation to final production, we adhere to the highest standards.
- Specialized Process Capabilities:We have the capability to handle complex structures such as microvias, blind vias, and buried vias, catering to high-density layouts and fine trace routing requirements. We also utilize various surface finishing techniques such as ENIG (Electroless Nickel Immersion Gold), OSP (Organic Solderability Preservatives), etc., to ensure corrosion resistance and excellent solderability.
- Quality Assurance and Testing:Throughout the production process, we conduct rigorous electrical testing and visual inspections to ensure the stability and reliability of each Megtron 6 PCB. Our quality assurance system guarantees that products meet stringent customer requirements before delivery.
With our expertise and commitment, we deliver high-quality Megtron 6 PCB materials that meet the design and manufacturing needs of various complex electronic products. Whether in telecommunications, computing, aerospace, or other industries, we provide reliable solutions to help customers achieve technological innovation and competitive advantage.
What are the 7 qualities of good customer service?
Good customer service is characterized by several key qualities that ensure customers feel valued, satisfied, and willing to continue doing business with a company. Here are seven essential qualities of good customer service:
- Responsiveness:A good customer service team responds promptly to customer inquiries, concerns, and requests. This includes acknowledging messages, answering calls promptly, and providing timely resolutions to issues.
- Empathy:Effective customer service representatives empathize with customers’ situations and emotions. They listen actively, understand the customer’s perspective, and show genuine concern for their needs or challenges.
- Clarity:Clear communication is crucial in customer service interactions. Representatives should articulate information clearly, avoid jargon or technical language that customers may not understand, and ensure that explanations and instructions are easy to follow.
- Professionalism:Professionalism encompasses maintaining a courteous and respectful demeanor at all times. Customer service representatives should conduct themselves professionally, remain calm under pressure, and handle challenging situations with composure.
- Knowledgeability: Good customer service requires a thorough understanding of the company’s products, services, policies, and processes. Representatives should possess adequate knowledge to provide accurate information, address inquiries, and assist customers effectively.
- Problem-solving Skills:Customers often seek assistance to resolve issues or challenges. Effective customer service involves having strong problem-solving abilities to identify root causes, explore solutions, and implement appropriate actions to resolve issues satisfactorily.
- Personalization:Tailoring interactions to individual customer needs and preferences enhances the customer experience. Good customer service involves recognizing repeat customers, remembering their preferences, and offering personalized solutions or recommendations whenever possible.
By embodying these qualities, organizations can foster positive customer relationships, build trust and loyalty, and differentiate themselves in competitive markets based on superior customer service experiences.
FAQs
What are Megtron 6 materials PCBs used for?
Megtron 6 PCBs are used in high-performance applications requiring excellent signal integrity, low loss, and thermal reliability. They are ideal for high-speed digital designs, RF (Radio Frequency) circuits, and applications where maintaining signal quality over a wide frequency range is critical.
What are the key advantages of Megtron 6 materials?
Megtron 6 materials offer advantages such as stable electrical properties (low Df and stable dielectric constant), high thermal reliability, and good mechanical strength. These properties make them suitable for complex and demanding electronic designs.
How do Megtron 6 materials compare to standard PCB materials like FR-4?
Compared to standard PCB materials like FR-4, Megtron 6 materials provide superior electrical performance, especially at higher frequencies. They have lower loss tangent (Df), better thermal stability, and enhanced signal transmission capabilities.
What are the considerations when designing with Megtron 6 materials?
Design considerations include impedance control, layer stackup optimization for signal integrity, proper via design (including microvias for high-density layouts), and selecting appropriate surface finishes to ensure reliability and performance.
Is Megtron 6 suitable for high-frequency and high-speed applications?
Yes, Megtron 6 materials are specifically designed for high-frequency and high-speed applications. They support the transmission of signals with minimal loss and distortion, making them suitable for telecommunications, computing, aerospace, and other advanced electronics.
How can I ensure quality when using Megtron 6 materials PCBs?
Ensuring quality involves working with experienced PCB manufacturers who are familiar with handling Megtron 6 materials. It’s important to specify design requirements accurately, conduct thorough testing for signal integrity, and verify compliance with industry standards.
What surface finishes are compatible with Megtron 6 materials?
Common surface finishes for Megtron 6 PCBs include Electroless Nickel Immersion Gold (ENIG), Organic Solderability Preservatives (OSP), and Hot Air Solder Leveling (HASL). The choice of surface finish depends on specific application requirements and soldering processes.