Microtrace LED PCB Manufacturer
Microtrace LED PCB Manufacturer,Microtrace LED PCBs revolutionize the realm of lighting and display technology with their compact size and high pixel density. Integrating micro-sized LED chips, these PCBs offer enhanced brightness, energy efficiency, and intricate designs suitable for various applications. Their advanced design allows for the creation of vibrant LED displays, captivating signage, and innovative lighting fixtures with unparalleled detail and clarity. Manufactured with precision and expertise, Microtrace LED PCBs undergo meticulous fabrication processes, including laser drilling and surface-mount assembly, ensuring optimal performance and reliability. With their ability to deliver stunning visuals, superior energy efficiency, and versatility, Microtrace LED PCBs are at the forefront of the lighting and display industry, empowering designers to push the boundaries of creativity and innovation.
What is a Microtrace LED PCB?
A Microtrace LED PCB is a type of printed circuit board (PCB) that integrates micro-sized LED chips. These LED chips are typically much smaller than traditional LEDs, allowing for higher pixel density and more intricate designs in applications such as LED displays, signage, and lighting fixtures.
Microtrace LED PCBs are often used in products where space is limited or where a finer resolution is required. They offer advantages such as better energy efficiency, enhanced brightness, and the ability to create more detailed images or patterns due to their compact size and high density.
These PCBs usually require specialized manufacturing processes to ensure precise placement and connection of the micro-sized LED chips. Additionally, they may incorporate technologies like surface-mount device (SMD) assembly and fine-pitch soldering techniques to achieve the desired performance and reliability.
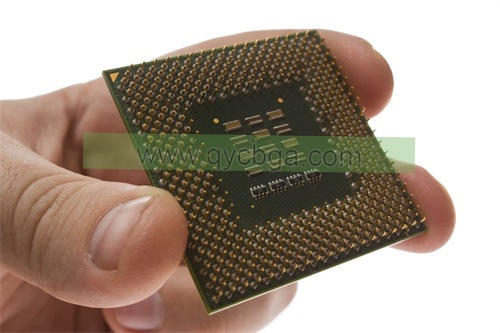
Microtrace LED PCB Manufacturer
What are the Microtrace LED PCB Design Guidelines?
Designing a Microtrace LED PCB involves considerations to ensure optimal performance and reliability. While specific guidelines may vary depending on the manufacturer and application requirements, here are some general design considerations:
- LED Selection: Choose LEDs with appropriate specifications for your application, including color, brightness, viewing angle, and forward voltage/current ratings. Ensure compatibility with the PCB layout and assembly process.
- PCB Layout: Design the PCB layout to accommodate the desired LED density and arrangement. Consider factors such as spacing between LEDs, trace routing, and thermal management to prevent overheating.
- Trace Width and Spacing: Use appropriate trace widths and spacing to handle the current requirements of the LEDs and minimize voltage drop. Calculate trace widths based on the maximum current and copper thickness to avoid overheating and ensure reliable operation.
- Power Distribution: Implement a robust power distribution network to ensure uniform brightness and color consistency across all LEDs. Use power planes or wide traces to minimize voltage drop and thermal issues.
- Grounding: Implement a solid ground plane to minimize electrical noise and interference. Connect all ground pins of the LEDs to the ground plane using low-impedance traces or vias.
- Signal Integrity: Minimize signal degradation by optimizing trace lengths and impedance matching techniques. Ensure that high-speed data signals (if applicable) maintain signal integrity throughout the PCB.
- Thermal Management: Incorporate thermal vias, heatsinks, or other cooling mechanisms to dissipate heat generated by the LEDs. Proper thermal management is crucial for maintaining LED performance and reliability.
- Manufacturability: Design the PCB with manufacturability in mind, considering factors such as assembly process compatibility, component placement, and solder mask design. Ensure that the design meets the capabilities of your chosen PCB fabrication and assembly processes.
- Testing and Quality Control: Plan for testing and quality control procedures to verify the functionality and performance of the LED PCB. Consider implementing test points, fiducial markers, and other features to facilitate testing and inspection during manufacturing.
- Environmental Considerations: Select materials and components that can withstand the environmental conditions of the intended application, including temperature, humidity, and vibration.
By following these guidelines and working closely with manufacturers and engineers experienced in Microtrace LED PCB design, you can ensure the successful development of high-performance and reliable LED-based products.
What is the Microtrace LED PCB Fabrication Process?
The fabrication process for Microtrace LED PCBs involves several steps, including design, material selection, manufacturing, and testing. Here’s an overview of the typical fabrication process:
- Design: The process begins with the design of the PCB layout, including the placement of micro-sized LED chips, routing of electrical traces, and incorporation of necessary features for power distribution, signal integrity, and thermal management. Design software such as Altium Designer or Cadence Allegro is commonly used for this purpose.
- Material Selection: Select appropriate materials for the PCB substrate, copper layers, solder mask, and other components based on the desired performance characteristics and environmental requirements. High-quality materials with good thermal conductivity and electrical insulation properties are essential for Microtrace LED PCBs.
- Manufacturing Preparation: Once the design is finalized, the fabrication process begins with the preparation of the manufacturing equipment and materials. This includes preparing the PCB substrate, applying copper layers through processes like electroplating or lamination, and preparing solder mask layers.
- Laser Drilling: Microtrace LED PCBs often require precision drilling of tiny holes to accommodate the micro-sized LED chips. Laser drilling is commonly used for this purpose due to its accuracy and ability to produce small-diameter holes with minimal thermal damage to surrounding materials.
- Solder Mask Application: Apply solder mask to the PCB surface to protect the copper traces and pads from oxidation, environmental damage, and solder bridging during assembly. Solder mask is typically applied using screen printing or spray coating methods.
- LED Placement and Soldering: Place the micro-sized LED chips onto the PCB according to the designed layout. This process may involve automated pick-and-place machines to ensure precise placement. Once positioned, the LEDs are soldered to the PCB using reflow soldering techniques, which involve heating the PCB to melt the solder and create a secure electrical connection.
- Testing and Inspection: After soldering, the PCBs undergo testing and inspection to verify the functionality and quality of the assembled LEDs. This may include electrical testing to ensure proper connectivity and brightness uniformity, as well as visual inspection to check for defects such as solder bridges or misaligned components.
- Finishing Processes: Once testing is complete and any defects are addressed, the PCBs may undergo additional finishing processes such as surface treatment or coating to improve durability, corrosion resistance, and solderability.
- Packaging and Shipping: Finally, the finished Microtrace LED PCBs are packaged according to customer specifications and shipped to their destination for incorporation into LED displays, signage, lighting fixtures, or other applications.
Throughout the fabrication process, quality control measures are implemented to ensure that the finished PCBs meet the required specifications for performance, reliability, and consistency. Collaboration between design engineers, manufacturers, and quality assurance teams is essential to achieving successful fabrication of Microtrace LED PCBs.
How do you manufacture a Microtrace LED PCB?
Manufacturing a Microtrace LED PCB involves several key steps, including design, material selection, PCB fabrication, LED assembly, and testing. Here’s a detailed overview of the manufacturing process:
- Design: The process begins with designing the PCB layout, including the arrangement of micro-sized LED chips, routing of electrical traces, and integration of necessary features for power distribution, signal integrity, and thermal management. Design software like Altium Designer or Cadence Allegro is commonly used for this purpose.
- Material Selection: Choose appropriate materials for the PCB substrate, copper layers, solder mask, and other components based on the desired performance characteristics and environmental requirements. High-quality materials with good thermal conductivity and electrical insulation properties are essential for Microtrace LED PCBs.
- PCB Fabrication: The fabrication process starts with preparing the PCB substrate, typically made of materials like FR-4 (fiberglass-reinforced epoxy laminate). Copper layers are then applied to the substrate through processes like electroplating or lamination. The PCB is then etched to remove unwanted copper, leaving behind the desired circuit traces.
- Laser Drilling: Microtrace LED PCBs often require precision drilling of tiny holes to accommodate the micro-sized LED chips. Laser drilling is commonly used for this purpose due to its accuracy and ability to produce small-diameter holes with minimal thermal damage to surrounding materials.
- Solder Mask Application: Apply solder mask to the PCB surface to protect the copper traces and pads from oxidation, environmental damage, and solder bridging during assembly. Solder mask is typically applied using screen printing or spray coating methods.
- LED Assembly: Place the micro-sized LED chips onto the PCB according to the designed layout. This process may involve automated pick-and-place machines to ensure precise placement. Once positioned, the LEDs are soldered to the PCB using reflow soldering techniques, which involve heating the PCB to melt the solder and create a secure electrical connection.
- Testing and Inspection: After soldering, the PCBs undergo testing and inspection to verify the functionality and quality of the assembled LEDs. This may include electrical testing to ensure proper connectivity and brightness uniformity, as well as visual inspection to check for defects such as solder bridges or misaligned components.
- Finishing Processes: Once testing is complete and any defects are addressed, the PCBs may undergo additional finishing processes such as surface treatment or coating to improve durability, corrosion resistance, and solderability.
- Packaging and Shipping: Finally, the finished Microtrace LED PCBs are packaged according to customer specifications and shipped to their destination for incorporation into LED displays, signage, lighting fixtures, or other applications.
Throughout the manufacturing process, quality control measures are implemented to ensure that the finished PCBs meet the required specifications for performance, reliability, and consistency. Collaboration between design engineers, manufacturers, and quality assurance teams is essential to achieving successful fabrication of Microtrace LED PCBs.
How much should a Microtrace LED PCB cost?
The cost of a Microtrace LED PCB can vary widely depending on several factors, including:
- Design Complexity: The complexity of the PCB layout, including the number of LED chips, their arrangement, trace routing, and additional features such as power distribution and thermal management, can significantly impact the cost.
- Material Selection: The choice of materials for the PCB substrate, copper layers, solder mask, and other components will affect the overall cost. High-quality materials with specific properties (e.g., thermal conductivity, electrical insulation) may be more expensive.
- Manufacturing Processes: The fabrication processes involved, such as laser drilling, surface treatment, and assembly techniques, can influence the cost. Advanced manufacturing techniques or specialized equipment may incur higher expenses.
- Quantities: Economies of scale apply in PCB manufacturing, meaning that larger production quantities typically result in lower per-unit costs. Ordering larger volumes can often reduce the cost per PCB.
- Supplier and Location: Different PCB manufacturers may offer varying pricing based on their capabilities, expertise, and location. Manufacturing costs can also vary depending on factors such as labor costs, overheads, and market conditions in different regions.
- Customization and Special Requirements: Customization, additional features, or specific requirements tailored to the application may incur extra costs. For example, if the Microtrace LED PCB needs to meet certain industry standards or environmental certifications, additional testing and compliance measures may be necessary.
Without specific details about the design, materials, manufacturing processes, and quantities involved, it’s challenging to provide an exact cost for a Microtrace LED PCB. However, for a rough estimate, you can expect the cost to range from a few dollars to several tens or even hundreds of dollars per unit, depending on the factors mentioned above. For accurate pricing, it’s best to consult with PCB manufacturers or suppliers and provide detailed specifications for a quote.
What is Microtrace LED PCB base material?
The base material for Microtrace LED PCBs typically consists of a substrate made from fiberglass-reinforced epoxy laminate, commonly known as FR-4. FR-4 is a widely used and cost-effective material for PCBs due to its excellent electrical insulation properties, mechanical strength, and thermal stability.
FR-4 is composed of layers of woven fiberglass cloth impregnated with epoxy resin. The layers are laminated together under heat and pressure to form a rigid substrate with good dimensional stability. Copper foil is then bonded to one or both sides of the FR-4 substrate to create the conductive traces and pads for the circuit.
In addition to FR-4, other base materials may be used for specialized applications or to meet specific performance requirements. For example:
- High-Temperature FR-4: FR-4 materials with higher glass transition temperatures (Tg) are available for applications requiring enhanced thermal performance and reliability at elevated temperatures.
- Metal Core PCBs (MCPCBs): For applications with high power dissipation requirements, Metal Core PCBs (MCPCBs) may be used, where a metal core (typically aluminum or copper) is used as the substrate instead of FR-4. The metal core provides better thermal conductivity, allowing for efficient heat dissipation from the LEDs.
- Flexible PCBs: Flexible PCB materials such as polyimide (PI) or polyester (PET) may be used for applications requiring bendable or conformal PCBs, such as flexible LED displays or lighting fixtures.
- High-Frequency PCBs: For applications involving high-frequency signals, such as radio frequency (RF) communication or microwave circuits, specialized high-frequency PCB materials with low dielectric constants and loss tangents may be used.
The choice of base material depends on factors such as the application requirements, thermal management needs, cost considerations, and manufacturing feasibility. Designers typically select the base material that best balances performance, cost, and manufacturability for the specific application of the Microtrace LED PCB.
Which company makes Microtrace LED PCBs?
There are many companies that manufacture Microtrace LED PCBs. Some well-known companies include Advanced Circuits in the United States, Nippon Mektron in Japan, and Korea Circuit in South Korea. These companies have advanced technology and equipment to produce high-quality Microtrace LED PCBs that meet various customer needs.
As for our company, we are also a professional PCB manufacturer with extensive experience and advanced manufacturing equipment. We have a highly skilled team, including engineers, technicians, and quality control experts, capable of providing customized solutions for Microtrace LED PCBs according to customer requirements.
Our company can provide the following services and advantages:
- Customized Design: We can provide customized Microtrace LED PCB design solutions based on customer requirements, including layout design, material selection, and circuit optimization.
- Advanced Manufacturing Equipment: We have advanced manufacturing equipment and technology, including high-precision laser drilling machines, automated pick-and-place equipment, and advanced surface treatment and soldering equipment, ensuring the quality and stability of PCB manufacturing.
- Strict Quality Control: We implement strict quality control procedures, conducting rigorous inspections and testing at every stage of the production process from raw material procurement to manufacturing, to ensure the production of high-quality Microtrace LED PCBs that meet customer requirements.
- Timely Delivery and Excellent Customer Service: We are committed to providing timely and efficient services, maintaining communication and collaboration with customers throughout the production process, and ensuring on-time delivery of products that meet customer needs.
With our company’s technical strength, professional team, and quality service, we are confident in producing high-quality, high-performance Microtrace LED PCBs that meet various customer needs and provide support and assurance for the success of our customers’ projects.
What are the 7 qualities of good customer service?
Good customer service is characterized by several key qualities that help foster positive relationships with customers and enhance their overall experience. Here are seven qualities of good customer service:
- Empathy: Empathy involves understanding and sharing the feelings of customers. Good customer service representatives listen actively to customers’ concerns, acknowledge their emotions, and demonstrate empathy by showing genuine care and concern.
- Responsiveness: Responsiveness refers to the ability to address customer inquiries, requests, and issues promptly. Good customer service involves providing timely responses to customer inquiries, whether it’s answering questions, resolving problems, or providing assistance.
- Professionalism:Professionalism entails maintaining a courteous, respectful, and professional demeanor when interacting with customers. Good customer service representatives exhibit professionalism through their communication, behavior, and actions, regardless of the situation.
- Knowledgeability: Knowledgeability involves having a deep understanding of the products or services offered by the company, as well as the ability to provide accurate and helpful information to customers. Good customer service representatives are knowledgeable about the products, policies, and procedures of the company and can effectively address customer inquiries and concerns.
- Adaptability: Adaptability refers to the ability to adjust and tailor interactions to meet the unique needs and preferences of individual customers. Good customer service representatives are flexible and adaptable, capable of customizing their approach based on the customer’s communication style, personality, and specific situation.
- Problem-Solving Skills: Problem-solving skills are essential for effectively resolving customer issues and addressing their concerns. Good customer service representatives can identify and analyze problems, propose appropriate solutions, and follow through to ensure customer satisfaction.
- Consistency: Consistency involves delivering a consistently high level of service across all customer interactions and touchpoints. Good customer service is reliable and consistent, ensuring that customers receive the same positive experience every time they interact with the company.
By embodying these qualities, businesses can cultivate strong customer relationships, build trust and loyalty, and differentiate themselves in the competitive marketplace.
FAQs
What are Microtrace LED PCBs?
Microtrace LED PCBs are printed circuit boards that integrate micro-sized LED chips. These LED chips are smaller than traditional LEDs, allowing for higher pixel density and more intricate designs in applications such as LED displays, signage, and lighting fixtures.
What are the advantages of Microtrace LED PCBs?
Some advantages of Microtrace LED PCBs include higher pixel density, enhanced brightness, better energy efficiency, and the ability to create more detailed images or patterns due to their compact size and high density.
How are Microtrace LED PCBs manufactured?
The manufacturing process for Microtrace LED PCBs involves several steps, including design, material selection, PCB fabrication, LED assembly, and testing. This process requires specialized equipment and expertise to ensure precise placement and connection of the micro-sized LED chips.
What are the key design considerations for Microtrace LED PCBs?
Key design considerations for Microtrace LED PCBs include LED selection, PCB layout, trace width and spacing, power distribution, grounding, signal integrity, thermal management, manufacturability, testing, and environmental considerations.
What materials are used in Microtrace LED PCBs?
The base material for Microtrace LED PCBs typically consists of a substrate made from fiberglass-reinforced epoxy laminate (FR-4). Other materials such as high-temperature FR-4, metal core PCBs (MCPCBs), and flexible PCBs may be used for specialized applications or to meet specific performance requirements.
What companies manufacture Microtrace LED PCBs?
Companies that manufacture Microtrace LED PCBs include Advanced Circuits, Nippon Mektron, Korea Circuit, and others. These companies have advanced technology and expertise in producing high-quality Microtrace LED PCBs for various applications.
How much do Microtrace LED PCBs cost?
The cost of Microtrace LED PCBs can vary depending on factors such as design complexity, material selection, manufacturing processes, quantities, supplier, and customization requirements. It’s best to consult with PCB manufacturers or suppliers to obtain accurate pricing based on specific project needs.