RF Antenna Substrate Manufacturer
RF Antenna Substrate Manufacturer,RF antenna substrates are critical components used in the manufacturing of radio frequency (RF) antennas, providing support and a foundation for antennas. These substrates are typically made from high-performance materials such as fiberglass-reinforced epoxy (FR4), Rogers laminates, ceramics, or polytetrafluoroethylene (PTFE). The choice of RF antenna substrate is crucial for antenna performance and characteristics as it affects key parameters such as dielectric constant, loss tangent, mechanical stability, and thermal properties. Fabricating RF antenna substrates involves multiple process steps including material preparation, shaping, surface treatment, metal deposition, pattern definition, and quality control. These substrates can be customized to meet the requirements of specific applications, accommodating different frequencies, powers, sizes, and environmental conditions. In summary, RF antenna substrates are essential components for achieving high performance and reliable wireless communication systems, with their quality and performance directly impacting the overall system performance and reliability.
What is RF Antenna substrate?
RF antenna substrate refers to the material on which radio frequency (RF) antennas are fabricated or mounted. This substrate plays a crucial role in the performance of the antenna. The choice of substrate material can affect parameters such as the antenna’s efficiency, bandwidth, and radiation pattern.
Common materials used for RF antenna substrates include:
- FR4: This is a common substrate material made from a woven fiberglass cloth impregnated with an epoxy resin binder. FR4 is widely used due to its low cost, good electrical properties, and ease of fabrication.
- Rogers RO4003: Rogers Corporation manufactures high-frequency laminates specifically designed for RF applications. RO4003 is one such material, offering excellent dielectric properties and stability at high frequencies.
- Polytetrafluoroethylene (PTFE):Known by the brand name Teflon, PTFE is a fluoropolymer that is used as a substrate material for high-frequency RF antennas. It has low dielectric loss and can maintain its properties over a wide range of temperatures.
- Ceramic: Some RF antennas use ceramic substrates, which offer high thermal conductivity and excellent mechanical stability. Ceramic substrates can be particularly useful in harsh environments.
- Liquid Crystal Polymer (LCP): LCP is a type of thermoplastic that is gaining popularity as a substrate material for RF antennas due to its low dielectric constant, low moisture absorption, and excellent dimensional stability.
The choice of substrate material depends on various factors such as the operating frequency of the antenna, environmental conditions, mechanical requirements, and cost considerations. Different substrates have different electrical properties, thermal properties, and fabrication characteristics, so it’s important to select the appropriate material based on the specific requirements of the antenna design.
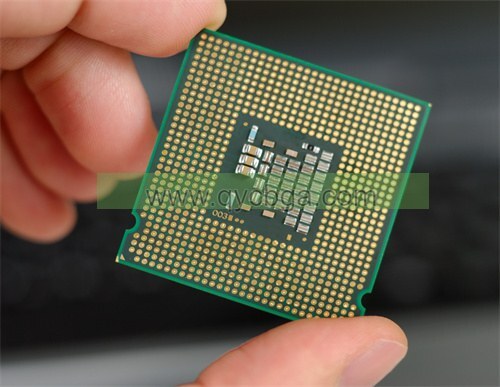
RF Antenna Substrate Manufacturer
What are RF Antenna substrate Design Guidelines?
Designing RF antennas on substrates requires careful consideration of various factors to ensure optimal performance. Here are some design guidelines for RF antenna substrates:
- Dielectric Constant (ε_r): The substrate’s dielectric constant influences the antenna’s impedance, radiation pattern, and bandwidth. Choose a substrate with a dielectric constant appropriate for the desired antenna characteristics. Lower dielectric constants generally result in wider bandwidth antennas.
- Loss Tangent (tan δ): Loss tangent affects the substrate’s lossiness and determines the antenna’s efficiency. Lower loss tangents are desirable for minimizing signal losses, especially at higher frequencies.
- Thickness: The substrate thickness affects the antenna’s radiation pattern and impedance. It’s typically chosen based on the desired operating frequency and mechanical considerations. Thinner substrates can lead to more compact antenna designs but may have mechanical limitations.
- Thermal Stability: Ensure that the substrate material can withstand the anticipated operating temperatures without significant degradation in electrical properties.
- Mechanical Stability: Choose a substrate with appropriate mechanical strength and dimensional stability to withstand environmental factors such as vibration, shock, and thermal cycling.
- Surface Roughness: Smooth substrate surfaces are essential for maintaining good adhesion between metal traces and minimizing losses due to surface roughness. Surface roughness can affect the antenna’s performance, especially at higher frequencies.
- Cost: Consider the cost of the substrate material, especially for mass-produced antennas. Balance performance requirements with cost considerations to achieve a cost-effective solution.
- Manufacturability: Select a substrate material that is compatible with the chosen manufacturing processes, such as etching, printing, or milling. Ensure that the substrate can be easily processed into the desired antenna shape and dimensions.
- Environmental Considerations: Evaluate the substrate’s resistance to moisture, chemicals, UV radiation, and other environmental factors relevant to the antenna’s intended application.
- Electromagnetic Compatibility (EMC): Ensure that the substrate material does not interfere with the antenna’s electromagnetic performance or cause electromagnetic interference with other nearby components or systems.
By following these guidelines and carefully selecting the appropriate substrate material, designers can create RF antennas that meet performance requirements while considering factors such as cost, manufacturability, and environmental durability.
What is the RF Antenna substrate Fabrication Process?
The fabrication process for RF antennas on substrates typically involves several steps, including substrate preparation, antenna design and layout, material deposition, and post-processing. Here’s a general overview of the RF antenna substrate fabrication process:
- Substrate Selection: Choose a substrate material based on the antenna’s requirements, considering factors such as dielectric constant, loss tangent, mechanical properties, and cost.
- Substrate Preparation: Prepare the substrate surface by cleaning and, if necessary, roughening or treating it to ensure good adhesion of the antenna’s metal traces.
- Antenna Design and Layout: Design the antenna layout using simulation software or analytical tools to determine the optimal antenna geometry for the desired performance characteristics, such as frequency response, radiation pattern, and impedance matching.
- Metal Deposition: Deposit metal traces onto the substrate using techniques such as printing, sputtering, evaporation, or plating. The choice of deposition method depends on factors such as the substrate material, desired trace thickness, and manufacturing scale.
- Pattern Definition: Define the antenna pattern by selectively removing or masking the deposited metal traces using processes such as photolithography, etching, laser ablation, or milling. This step defines the antenna’s geometry and ensures that only the desired conductive paths remain on the substrate.
- Dielectric Layer Deposition (Optional): Deposit additional dielectric layers on the substrate to provide insulation between antenna elements or to enhance mechanical stability and environmental protection.
- Post-Processing: Perform any necessary post-processing steps, such as curing, annealing, surface coating, or encapsulation, to improve the antenna’s performance, durability, and environmental resistance.
- Testing and Characterization: Test the fabricated antenna to verify its performance against the design specifications. This may involve measurements of parameters such as return loss, radiation pattern, impedance matching, and bandwidth.
- Integration: Integrate the fabricated antenna into the final product or system, considering factors such as mechanical mounting, electrical connections, and electromagnetic compatibility with other components.
- Quality Control: Conduct quality control checks throughout the fabrication process to ensure that the antennas meet the required standards for performance, reliability, and consistency.
By following these steps and carefully controlling each stage of the fabrication process, manufacturers can produce RF antennas on substrates with the desired performance characteristics for a wide range of applications, including wireless communication, radar, sensing, and IoT devices.
How do you manufacture RF Antenna substrate?
Manufacturing RF antenna substrates involves processes to create the material used as the foundation for fabricating RF antennas. Here’s a general overview of how RF antenna substrates are manufactured:
- Material Selection: Choose the appropriate raw materials based on the desired properties of the substrate, such as dielectric constant, thermal stability, mechanical strength, and cost. Common substrate materials include fiberglass-reinforced epoxy (FR4), Rogers laminates, ceramics, and liquid crystal polymers (LCP).
- Preparation of Substrate Material:
– For materials like FR4: Fiberglass cloth is impregnated with an epoxy resin binder to create the substrate material. The resin may be mixed with additives to achieve specific properties.
– For laminates: Layers of different materials are combined under controlled conditions to create the laminate substrate, which typically consists of a dielectric layer sandwiched between conductive layers.
- Formulation and Mixing: If necessary, the raw materials are formulated and mixed according to specific recipes to achieve the desired material properties. This step may involve mixing resins, fillers, reinforcing fibers, and other additives in precise proportions.
- Curing or Polymerization: The mixed material is subjected to a curing or polymerization process to solidify it into the desired substrate form. This process may involve heat, pressure, or chemical catalysts to initiate and control the polymerization reaction.
- Shaping and Sizing: The cured substrate material is shaped and sized according to the requirements of the application. This may involve cutting, grinding, or machining the material into sheets, panels, or other forms suitable for further processing.
- Surface Treatment: The substrate surface may undergo treatment to improve adhesion, smoothness, or other surface properties. This may include cleaning, sanding, or applying surface coatings to enhance performance or facilitate subsequent manufacturing steps.
- Quality Control: Throughout the manufacturing process, quality control measures are implemented to ensure that the substrate material meets the required specifications for properties such as thickness, dielectric constant, mechanical strength, and surface quality.
- Packaging and Storage:Once manufactured, the RF antenna substrates are packaged and stored under controlled conditions to prevent contamination, moisture absorption, or other factors that could degrade their performance.
- Distribution:The manufactured RF antenna substrates are distributed to antenna manufacturers or other customers who will use them to fabricate RF antennas for various applications.
By following these manufacturing processes with precision and attention to detail, manufacturers can produce high-quality RF antenna substrates that meet the demanding requirements of modern wireless communication systems, radar systems, and other RF applications.
How much should RF Antenna substrate cost?
The cost of RF antenna substrate can vary widely depending on several factors, including the material used, manufacturing process, quality, quantity ordered, and supplier. Here are some general considerations regarding the cost of RF antenna substrates:
- Material Cost: Different substrate materials have varying costs. For example, common materials like FR4 may be more cost-effective compared to specialized materials like high-frequency laminates or ceramic substrates.
- Manufacturing Process: The complexity of the manufacturing process can influence the cost. For example, substrates that require specialized formulations, curing processes, or surface treatments may incur higher manufacturing costs.
- Quality and Performance: Higher-quality substrates with superior electrical properties, mechanical stability, and environmental resistance may command a higher price compared to lower-quality alternatives.
- Quantity Ordered: Bulk orders typically result in lower unit costs due to economies of scale. Larger quantities may qualify for volume discounts from suppliers.
- Supplier Pricing: Prices can vary between different suppliers based on factors such as location, production capabilities, overhead costs, and market competition.
- Customization: Customized substrates tailored to specific requirements may incur additional costs compared to off-the-shelf options.
- Packaging and Shipping: Additional costs such as packaging, handling, and shipping may contribute to the overall cost, especially for international orders.
- Market Demand: Fluctuations in market demand and supply can impact substrate prices. Materials in high demand or with limited availability may be priced higher.
It’s essential for buyers to consider these factors and evaluate their specific requirements when assessing the cost of RF antenna substrates. While cost is an important consideration, it’s also crucial to prioritize quality, performance, and reliability to ensure the overall success of the antenna design and application.
What is RF Antenna substrate base material?
The base material used for RF antenna substrates can vary depending on the specific requirements of the antenna design and the application. Some common base materials used for RF antenna substrates include:
- Fiberglass-Reinforced Epoxy (FR4): FR4 is a widely used substrate material for RF antennas due to its low cost, good electrical properties, mechanical strength, and ease of fabrication. It consists of a woven fiberglass cloth impregnated with an epoxy resin binder.
- Rogers Laminates: Rogers Corporation produces a range of high-frequency laminates specifically designed for RF applications. These laminates often have lower dielectric constants, lower loss tangents, and better stability at high frequencies compared to FR4, making them suitable for demanding RF antenna designs.
- Ceramics: Certain RF antennas may use ceramic substrates, which offer high thermal conductivity, excellent mechanical stability, and low dielectric loss. Ceramic substrates are particularly suitable for high-power RF applications and harsh environmental conditions.
- Polytetrafluoroethylene (PTFE): PTFE-based materials, such as Teflon, are known for their low dielectric constant, low loss tangent, and excellent electrical properties at high frequencies. PTFE substrates are commonly used in RF antennas where minimal signal loss and high performance are critical.
- Liquid Crystal Polymer (LCP): LCP is a type of thermoplastic material with low dielectric constant, low moisture absorption, and excellent dimensional stability. LCP substrates are gaining popularity for RF antennas, especially in applications requiring high-frequency operation and miniaturization.
- Metal-Backed Substrates: In some cases, RF antennas are fabricated on metal-backed substrates to provide enhanced mechanical stability and heat dissipation. Metal-backed substrates can also serve as ground planes for certain antenna designs.
The choice of base material depends on various factors such as the operating frequency, bandwidth, power requirements, environmental conditions, and cost considerations. Designers typically select the substrate material that best balances these factors to achieve the desired performance and reliability for the RF antenna application.
Which company manufactures RF Antenna substrate?
Several companies produce RF antenna substrates, including Rogers Corporation, DuPont, Isola Group, Taconic Advanced Dielectric Division, and Arlon Electronic Materials. These companies specialize in the development and manufacturing of high-performance substrate materials for wireless communication, radar systems, and other RF applications.
As for our company, we also have the capability to manufacture RF antenna substrates. We possess advanced production equipment and a skilled technical team dedicated to research and manufacture high-quality substrate materials that meet the needs of our customers. Our production process adheres strictly to quality management systems to ensure that our products meet the highest performance standards.
Here are some features of RF antenna substrates produced by our company:
- High-Quality Materials: We use premium substrate materials such as FR4, Rogers Laminates, ceramics, PTFE, and LCP to ensure that our antenna substrates exhibit excellent electrical properties, mechanical stability, and durability.
- Advanced Processes: We employ advanced production processes and equipment, including material preparation, surface treatment, metal deposition, and pattern definition, to ensure the accuracy and consistency of our antenna substrates.
- Customization Services: We offer customization services to tailor RF antenna substrates according to our customers’ specific requirements, including material selection, size customization, pattern design, and surface treatment, to meet the demands of various applications.
- Quality Assurance: We rigorously control every aspect of the production process and conduct strict quality checks and testing to ensure that each batch of our products meets our customers’ specifications and performance standards.
Through our RF antenna substrates, customers can obtain high-quality, reliable, and high-performance substrate materials to achieve success in their RF antenna designs. We are committed to providing excellent products and services to our customers and becoming their trusted partner.
What are the 7 qualities of good customer service?
Good customer service is characterized by several key qualities that contribute to a positive customer experience. Here are seven qualities of good customer service:
- Responsiveness: Good customer service involves being prompt and attentive to customers’ needs and inquiries. Responding to customer queries, requests, and issues in a timely manner demonstrates that their concerns are valued and addressed promptly.
- Empathy: Empathy is the ability to understand and share the feelings of others. Good customer service representatives empathize with customers, acknowledging their emotions, concerns, and frustrations. By showing empathy, they can build rapport, establish trust, and create a more positive interaction.
- Clear Communication: Effective communication is essential for providing good customer service. Customer service representatives should communicate clearly, using language that is easy to understand and avoiding jargon or technical terms that may confuse customers. They should listen actively to customers’ concerns and provide relevant information and solutions in a concise and understandable manner.
- Problem-Solving Skills: Good customer service involves the ability to identify and resolve customer issues effectively. Customer service representatives should have strong problem-solving skills, enabling them to analyze situations, evaluate options, and implement solutions that meet customers’ needs and expectations.
- Professionalism: Professionalism encompasses various aspects of behavior, including courtesy, respect, and integrity. Customer service representatives should conduct themselves professionally at all times, treating customers with respect and dignity, maintaining confidentiality, and upholding ethical standards.
- Product Knowledge: Good customer service requires a thorough understanding of the products or services offered by the company. Customer service representatives should be knowledgeable about the features, benefits, and specifications of the products or services they support. This enables them to provide accurate information, answer questions, and assist customers effectively.
- Follow-Up and Follow-Through: Providing good customer service doesn’t end with the initial interaction. Follow-up and follow-through are crucial for ensuring customer satisfaction and loyalty. Customer service representatives should follow up with customers to ensure that their issues have been resolved satisfactorily and offer assistance or additional support as needed. Consistent follow-through demonstrates commitment to customer satisfaction and helps build long-term relationships with customers.
By embodying these qualities, companies can deliver exceptional customer service experiences that leave a positive impression on customers and contribute to their overall satisfaction and loyalty.
FAQs
What is an RF antenna substrate?
An RF antenna substrate is the material on which radio frequency (RF) antennas are fabricated or mounted. It plays a crucial role in determining the antenna’s performance and characteristics.
What are common materials used for RF antenna substrates?
Common materials include fiberglass-reinforced epoxy (FR4), Rogers laminates, ceramics, polytetrafluoroethylene (PTFE), liquid crystal polymers (LCP), and metal-backed substrates.
How does the choice of substrate material affect antenna performance?
The substrate material influences parameters such as dielectric constant, loss tangent, mechanical stability, and thermal properties, which in turn affect the antenna’s impedance, bandwidth, efficiency, and radiation pattern.
What factors should be considered when selecting an RF antenna substrate?
Factors to consider include operating frequency, bandwidth, power requirements, mechanical strength, thermal stability, environmental conditions, and cost.
What are the fabrication processes involved in manufacturing RF antenna substrates?
Fabrication processes may include material preparation, shaping, surface treatment, metal deposition, pattern definition, curing or polymerization, and quality control measures.
How can I ensure the quality of RF antenna substrates?
Quality can be ensured by selecting reputable suppliers, specifying material requirements, conducting thorough testing and inspection, and adhering to industry standards and best practices.
Can RF antenna substrates be customized for specific applications?
Yes, many suppliers offer customization options such as material selection, size customization, surface treatment, and pattern design to meet the unique requirements of different applications.