Semiconductor Substrate Manufacturers
Semiconductor Substrate Manufacturers,Semiconductor substrates are foundational materials used in the fabrication of electronic devices. Comprising materials like silicon, gallium arsenide, or sapphire, these substrates provide a platform for the deposition and integration of semiconductor materials and components. They serve as the base upon which intricate semiconductor structures are built, enabling the creation of microchips, LEDs, and other electronic components. With precise material properties and surface characteristics, semiconductor substrates play a crucial role in determining the performance and reliability of semiconductor devices in various applications, from consumer electronics to telecommunications and beyond.
What is a Semiconductor Substrate?
A semiconductor substrate is a foundational material used in the fabrication of electronic and photonic devices. It primarily consists of semiconducting materials like silicon, gallium arsenide, or silicon carbide. These substrates serve as the base upon which various microelectronic devices, such as transistors, diodes, and integrated circuits, are built.
The process begins with the creation of a highly pure, single-crystal semiconductor wafer. This wafer provides a defect-free, uniform surface essential for the subsequent deposition and patterning processes involved in device fabrication. The semiconductor properties of these materials—specifically their ability to conduct electricity under certain conditions—make them suitable for controlling electrical currents, which is critical for the functioning of electronic devices.
Silicon, due to its abundant availability, cost-effectiveness, and excellent semiconductor properties, is the most widely used material for substrates. Gallium arsenide, on the other hand, offers superior electron mobility, making it ideal for high-frequency and optoelectronic applications.
The preparation of semiconductor substrates involves several steps, including crystal growth, slicing, polishing, and doping. Doping introduces impurities into the semiconductor to modify its electrical properties, enabling the creation of p-type or n-type regions crucial for device functionality.
In modern technology, advancements in substrate engineering have led to the development of specialized substrates, such as silicon-on-insulator (SOI) and strained silicon, which enhance device performance by reducing power consumption and increasing speed. These innovations continue to drive progress in electronics, making semiconductor substrates a cornerstone of the semiconductor industry.
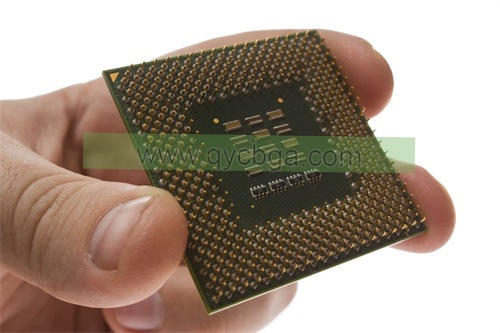
Semiconductor Substrate Manufacturers
What are Semiconductor Substrate Design Guidelines?
Semiconductor substrate design guidelines are a set of principles and practices aimed at optimizing the performance, reliability, and manufacturability of semiconductor devices. These guidelines are essential for engineers and designers involved in the development of semiconductor products. Here are some key aspects typically considered in semiconductor substrate design:
- Material Selection: Choose an appropriate semiconductor material based on the specific requirements of the device. Factors to consider include electrical properties (e.g., carrier mobility, bandgap), thermal conductivity, availability, and cost.
- Crystal Quality: Ensure high crystal quality to minimize defects and impurities, which can degrade device performance and reliability. Techniques such as crystal growth optimization and defect reduction are employed to enhance crystal quality.
- Surface Preparation:Achieve a smooth, clean substrate surface to facilitate subsequent processing steps like deposition and lithography. Surface polishing and cleaning techniques are employed to remove contaminants and irregularities.
- Doping Profile: Design the doping profile to create desired electrical characteristics, such as the formation of p-n junctions or modulation of carrier concentration. Precise control over dopant distribution is critical for achieving target device performance.
- Strain Engineering: Utilize strain engineering techniques to enhance carrier mobility and improve device performance. Strain can be induced in the substrate through methods like epitaxial growth or lattice mismatch.
- Dielectric Isolation: Implement dielectric isolation techniques to minimize parasitic effects and improve device isolation. Silicon-on-insulator (SOI) and trench isolation are common approaches used to achieve effective isolation between devices.
- Thermal Management: Address thermal issues by designing substrates with adequate thermal conductivity and heat dissipation capabilities. Efficient thermal management is crucial for preventing device overheating and ensuring long-term reliability.
- Integration Compatibility: Consider compatibility with existing semiconductor processes and integration schemes. Substrate designs should facilitate seamless integration with other device components and manufacturing processes.
- Scale-up Considerations: Anticipate scalability requirements by designing substrates suitable for large-scale production. Factors such as substrate size, yield optimization, and cost-effectiveness play a crucial role in scalability.
- Reliability and Yield: Design substrates with reliability and yield in mind to ensure consistent device performance and manufacturing success. Robust substrate designs minimize defects, variability, and reliability concerns.
By adhering to these semiconductor substrate design guidelines, engineers can develop substrates optimized for various applications, ranging from microprocessors and memory devices to sensors and optoelectronic components.
What is the Semiconductor Substrate Fabrication Process?
The semiconductor substrate fabrication process involves several steps to create the foundation upon which semiconductor devices are built. Here’s a simplified overview:
- Wafer Preparation: Silicon wafers are the most common substrate material used in semiconductor fabrication. The process begins with selecting high-purity silicon ingots, which are sliced into thin, flat discs called wafers. These wafers undergo cleaning and polishing to remove any impurities and defects.
- Oxidation: The wafer surface is oxidized to form a thin layer of silicon dioxide (SiO2) through a process called thermal oxidation. This oxide layer serves as an insulating material and can also act as a mask for subsequent etching steps.
- Photolithography:Photolithography involves transferring a pattern onto the wafer surface using light-sensitive photoresist materials. A photoresist layer is deposited onto the wafer, exposed to ultraviolet (UV) light through a photomask, and then developed to selectively remove the exposed areas, leaving behind the desired pattern.
- Etching: Etching is used to selectively remove material from the wafer surface based on the pattern defined by the photoresist. There are two main types of etching: wet etching, which uses liquid chemicals to dissolve the exposed material, and dry etching, which uses plasma to etch the material in a controlled manner.
- Doping: Doping involves introducing impurities into the wafer to modify its electrical properties. This is typically done through processes such as ion implantation or diffusion. Doping creates regions of different conductivity within the semiconductor substrate, essential for creating semiconductor devices such as transistors and diodes.
- Deposition: Thin films of various materials, such as metals or insulators, are deposited onto the wafer surface using techniques like physical vapor deposition (PVD) or chemical vapor deposition (CVD). These deposited layers are used to create interconnects, insulation layers, and other features in semiconductor devices.
- Annealing: Annealing is a heat treatment process used to activate dopant atoms, repair crystal damage caused by ion implantation, and improve the overall crystalline structure of the semiconductor material.
- Chemical Mechanical Polishing (CMP): CMP is used to planarize the wafer surface by removing excess material and achieving a smooth, flat surface. This step is crucial for ensuring uniformity and precision in subsequent device fabrication processes.
- Metrology and Inspection: Throughout the fabrication process, the wafers undergo various metrology and inspection steps to ensure dimensional accuracy, defect detection, and quality control.
By following these steps with precision and accuracy, semiconductor substrate fabrication creates the foundation for building intricate semiconductor devices used in a wide range of electronic applications.
How do you manufacture a Semiconductor Substrate?
Manufacturing a semiconductor substrate involves several intricate processes to produce a high-quality, defect-free material suitable for the fabrication of semiconductor devices. Here’s a generalized overview of the semiconductor substrate manufacturing process:
- Material Selection: Choose the appropriate semiconductor material based on the desired properties and applications of the final devices. Silicon (Si) is the most commonly used substrate material due to its abundance and well-understood properties. Other materials like gallium arsenide (GaAs) or silicon carbide (SiC) may be chosen for specific applications requiring unique properties.
- Crystal Growth: Grow a large, single-crystal ingot of the semiconductor material using methods like the Czochralski (CZ) or Float Zone (FZ) technique. In the CZ method, a seed crystal is slowly pulled from a molten semiconductor melt, allowing a single crystal to form as it solidifies. The FZ method involves passing a radiofrequency current through a polycrystalline rod, melting a small portion of it and allowing a single crystal to recrystallize.
- Ingot Cutting: Slice the grown ingot into thin wafers using diamond saws or wire saws. These wafers serve as the substrate for semiconductor device fabrication. The thickness of the wafers is typically a few hundred micrometers.
- Surface Preparation: Grind and polish the wafer surfaces to achieve a smooth and flat finish. This step removes surface defects and irregularities introduced during cutting and handling, ensuring uniformity across the wafer surface.
- Cleaning: Thoroughly clean the wafer surfaces to remove contaminants, particles, and residues. Cleaning processes may involve solvent cleaning, acid or alkaline treatments, and rinsing with deionized water to achieve high-purity surfaces.
- Doping: Introduce controlled amounts of dopant atoms into the semiconductor material to modify its electrical properties. Dopants such as boron, phosphorus, or arsenic are diffused or implanted into the wafer surface to create regions with specific conductivity types (p-type or n-type).
- Oxidation or Deposition: Optionally, oxidize the wafer surface to grow a thin layer of silicon dioxide (SiO2) through thermal oxidation. Alternatively, deposit thin films of various materials (e.g., silicon nitride, polysilicon) using techniques like chemical vapor deposition (CVD) or physical vapor deposition (PVD).
- Annealing:Subject the wafer to high-temperature annealing processes to activate dopants, repair crystal defects, and improve the quality of oxide layers. Annealing treatments may involve rapid thermal annealing (RTA) or furnace annealing in controlled atmospheres.
- Characterization: Perform various tests and analyses to evaluate the quality and properties of the semiconductor substrate. Techniques such as X-ray diffraction (XRD), scanning electron microscopy (SEM), and electrical measurements are used to assess crystal structure, surface morphology, and electrical characteristics.
- Packaging and Inspection: Package the processed wafers in protective carriers or cassettes to prevent contamination and damage. Conduct final visual inspections and quality checks to ensure compliance with specifications before shipment to semiconductor device manufacturers.
This summarized process outlines the key steps involved in manufacturing semiconductor substrates. Each step requires precise control and optimization to produce substrates with the desired properties for subsequent device fabrication. Additionally, advancements in semiconductor manufacturing technologies continue to refine and improve these processes for enhanced performance and reliability.
How much should a Semiconductor Substrate cost?
The cost of a semiconductor substrate can vary widely depending on several factors, including the material type, size, purity, and manufacturing complexity. Here are some key considerations that influence the cost:
- Material Type: Different semiconductor materials, such as silicon, gallium arsenide (GaAs), silicon carbide (SiC), and sapphire, have varying costs associated with their production and processing. Silicon wafers are the most common and cost-effective substrate material used in semiconductor fabrication.
- Size: The size of the semiconductor substrate, typically measured in diameter for wafers, directly affects the cost. Larger wafers provide more chips per wafer, leading to higher throughput and lower cost per chip. However, larger wafers also require more precise manufacturing processes and handling equipment, which can increase fabrication costs.
- Purity: The purity of the semiconductor substrate material is critical for device performance and reliability. Higher-purity substrates command higher prices due to the more stringent manufacturing processes and quality control measures required to achieve and maintain purity levels.
- Manufacturing Complexity: The complexity of the fabrication process, including the number of steps involved, the level of precision required, and the use of specialized techniques, can impact substrate costs. More complex substrates may require additional processing steps and incur higher manufacturing expenses.
- Supplier and Volume: The choice of supplier and the volume of substrates ordered can also affect costs. Larger orders may qualify for volume discounts, while sourcing from reputable suppliers known for high-quality substrates may command premium prices.
- Market Demand:Fluctuations in market demand and supply dynamics can influence substrate prices. During periods of high demand or supply shortages, substrate prices may increase, whereas oversupply situations can lead to price reductions.
- Technology Node:Semiconductor fabrication processes are continually advancing to smaller technology nodes, which require more advanced substrates with tighter specifications. Substrates for cutting-edge technology nodes may incur higher costs due to the investment in research, development, and manufacturing infrastructure required to produce them.
Overall, the cost of a semiconductor substrate can range from a few dollars to several hundred dollars or more per unit, depending on the aforementioned factors. It’s essential for semiconductor manufacturers to carefully consider their requirements and budget constraints when selecting substrates to ensure optimal performance and cost-effectiveness.
What is Semiconductor Substrate base material?
The base material for semiconductor substrates, particularly in the context of integrated circuit (IC) fabrication, is predominantly silicon. Silicon wafers serve as the foundational material upon which semiconductor devices are built. Silicon is chosen for its excellent semiconductor properties, including:
- Semiconductor Nature: Silicon is a semiconductor material, meaning it can conduct electricity under certain conditions but not as effectively as metals. This property is essential for creating electronic components like transistors, diodes, and integrated circuits.
- Abundance and Purity: Silicon is the second most abundant element in the Earth’s crust, making it readily available for large-scale semiconductor manufacturing. It can be refined to extremely high levels of purity, which is crucial for semiconductor device performance.
- Crystal Structure: Silicon has a crystalline structure that allows for precise control over its electrical properties. Silicon wafers are typically manufactured using a single crystal growth process, resulting in wafers with uniform crystal orientation and low defect density.
- Thermal Stability: Silicon exhibits excellent thermal stability, allowing semiconductor devices to operate reliably across a wide temperature range. This property is essential for maintaining device performance and reliability in various operating conditions.
While silicon is the most common substrate material, other semiconductor materials such as gallium arsenide (GaAs), silicon carbide (SiC), and sapphire are also used in specialized applications where their unique properties offer advantages over silicon. However, silicon remains the dominant substrate material in the semiconductor industry due to its abundance, well-established manufacturing processes, and versatility for a wide range of electronic devices.
Which company manufactures Semiconductor Substrates?
Semiconductor substrates are essential components in semiconductor manufacturing, and many companies specialize in their production. Some major semiconductor substrate manufacturers worldwide include Applied Materials, Lam Research, Entegris in the United States, Shin-Etsu Chemical and Toray Industries in Japan, LG Chem in South Korea, ASML in the Netherlands, and SCHOTT in Germany. These companies have extensive experience and advanced manufacturing technologies in the field of semiconductor substrates, capable of providing high-quality and high-performance substrate products.
As for our company, we have advanced semiconductor manufacturing equipment and a skilled technical team capable of producing semiconductor substrates. We employ strict quality control measures to ensure that our products meet customer requirements and standards. We can provide semiconductor substrates in various specifications and sizes to meet diverse application needs.
Our semiconductor substrate manufacturing process includes raw material procurement, processing, and quality inspection. We focus on technological innovation and continuous improvement to enhance production efficiency and product quality. Our team has rich experience and professional knowledge, capable of providing customized solutions and services according to customer needs.
As a company dedicated to semiconductor manufacturing, we are committed to providing high-quality, high-performance semiconductor substrate products and comprehensive support and services for customer business development. We look forward to cooperating with you to explore the future of the semiconductor industry.
What are the 7 qualities of good customer service?
Good customer service is characterized by several key qualities that contribute to positive interactions and customer satisfaction. Here are seven essential qualities:
- Empathy: Understanding and empathizing with customers’ needs and concerns fosters trust and helps build strong relationships. Empathetic customer service representatives listen actively, acknowledge customers’ emotions, and demonstrate genuine care and understanding.
- Communication Skills: Effective communication is crucial in conveying information clearly and resolving issues efficiently. Customer service representatives should be articulate, attentive, and responsive, ensuring that customers feel heard and valued throughout the interaction.
- Problem-solving Abilities: Good customer service representatives possess strong problem-solving skills, enabling them to address customer inquiries, resolve issues, and find solutions to challenges effectively. They approach problems with creativity, resourcefulness, and a commitment to customer satisfaction.
- Product Knowledge:Having comprehensive knowledge about products or services allows customer service representatives to provide accurate information, answer questions confidently, and offer relevant recommendations. A deep understanding of offerings instills trust and credibility with customers.
- Professionalism: Professionalism encompasses maintaining a courteous and respectful demeanor, even in challenging situations. Customer service representatives demonstrate professionalism through reliability, integrity, and accountability, ensuring consistent and positive interactions with customers.
- Adaptability: Being adaptable enables customer service representatives to respond flexibly to diverse customer needs, preferences, and situations. They adjust their approach, communication style, and problem-solving strategies accordingly, ensuring personalized and effective service.
- Follow-up and Feedback: Following up with customers after resolving inquiries or issues demonstrates commitment to their satisfaction. Seeking feedback from customers allows businesses to identify areas for improvement and continuously enhance the customer service experience.
By embodying these qualities, businesses can deliver exceptional customer service experiences that foster loyalty, retention, and positive word-of-mouth referrals.
FAQs (Frequently Asked Questions)
What is a semiconductor substrate?
A semiconductor substrate is the base material upon which semiconductor devices are built. It provides a foundation for the fabrication of integrated circuits (ICs) and other semiconductor components.
What materials are used for semiconductor substrates?
The most common material used for semiconductor substrates is silicon. Other materials, such as gallium arsenide (GaAs), silicon carbide (SiC), and sapphire, are also used in specialized applications.
What are the characteristics of a good semiconductor substrate?
Good semiconductor substrates should have high purity, uniform crystal structure, precise dimensions, and low defect density. These characteristics are essential for ensuring the performance and reliability of semiconductor devices.
How are semiconductor substrates manufactured?
Semiconductor substrates are typically manufactured through processes such as crystal growth, wafer slicing, polishing, and surface treatment. These processes are carried out with high precision and quality control to produce substrates with the desired properties.
What sizes are semiconductor substrates available in?
Semiconductor substrates are commonly available in the form of circular wafers with diameters ranging from a few inches to over 12 inches (300mm). The choice of wafer size depends on the specific requirements of the semiconductor manufacturing process.
What are some common applications of semiconductor substrates?
Semiconductor substrates are used in various applications, including integrated circuits (ICs), microprocessors, memory chips, sensors, photovoltaic cells, and light-emitting diodes (LEDs).
What factors affect the cost of semiconductor substrates?
The cost of semiconductor substrates depends on factors such as material type, size, purity, manufacturing complexity, supplier, and market demand. Larger, higher-purity substrates with advanced features typically command higher prices.
How are semiconductor substrates tested and inspected for quality?
Semiconductor substrates undergo rigorous testing and inspection processes to ensure quality and reliability. This includes measurements of dimensions, crystal quality, defect density, surface roughness, and electrical properties.