Ultra Thin hard PCB Manufacturer
Ultra Thin hard PCB Manufacturer,The Ultra Thin hard PCB is a specialized circuit board designed for applications requiring both rigidity and minimal thickness. These PCBs are manufactured using advanced materials and processes to achieve thicknesses as low as 0.1mm, while maintaining mechanical strength and durability. They offer excellent electrical performance and are ideal for use in compact electronic devices such as smartphones, tablets, and wearables, where space is at a premium. Ultra Thin hard PCBs support high-density component placement and provide reliable signal integrity. Their lightweight and slim profile make them perfect for modern, sleek device designs, ensuring both functionality and aesthetics.
What is an Ultra Thin Hard PCB?
An Ultra Thin Hard PCB (Printed Circuit Board) is a type of circuit board characterized by its exceptionally thin profile and rigid construction. Unlike standard PCBs, which may range from 0.8 mm to several millimeters in thickness, ultra-thin hard PCBs typically have a thickness of less than 0.2 mm. This reduced thickness makes them suitable for applications where space and weight constraints are critical.
The construction of ultra-thin hard PCBs involves using advanced materials and manufacturing techniques. The base material is often a high-quality epoxy resin or other rigid substrates that provide stability and durability despite the reduced thickness. These PCBs are designed to support the same functions as traditional PCBs, including electrical connections and signal transmission, but in a more compact form factor.
Key applications for ultra-thin hard PCBs include consumer electronics such as smartphones, wearables, and tablets, where their slim profile can be integrated into compact designs. They are also used in medical devices, automotive electronics, and other high-tech applications where both performance and space efficiency are required.
Manufacturing ultra-thin hard PCBs involves precise processing and handling to avoid damage, as the thin substrate can be more fragile compared to standard PCBs. Techniques such as laser drilling and advanced etching are employed to create the intricate circuit patterns needed for these boards.
In summary, ultra-thin hard PCBs combine thinness with rigidity to meet the demands of modern electronic devices, offering both performance and space efficiency.
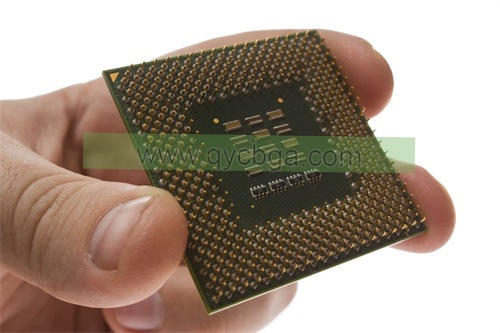
Ultra Thin hard PCB Manufacturer
What are the Ultra Thin Hard PCB Design Guidelines?
Designing ultra-thin hard PCBs requires specific guidelines to ensure performance, reliability, and manufacturability. Here are some key design guidelines:
- Material Selection: Choose high-quality, stable materials like epoxy resin with a low CTE (Coefficient of Thermal Expansion) to maintain structural integrity. Ensure the material can withstand the required thermal and electrical stresses.
- Layer Count: Minimize the number of layers where possible. Ultra-thin hard PCBs often use fewer layers to reduce thickness. For complex designs, balance layer count with the need for signal integrity and power distribution.
- Trace Width and Spacing:Design trace widths and spacings according to current-carrying requirements and manufacturing capabilities. Use software tools to ensure traces meet the minimum width and spacing requirements to avoid potential issues during fabrication.
- Via Sizes and Placement: Opt for smaller vias to save space. Blind and buried vias can be used to maintain the board’s thin profile while ensuring effective signal routing. Avoid excessive via usage, as it can compromise the board’s rigidity.
- Thermal Management: Implement heat dissipation techniques such as thermal vias or heat sinks if the design involves high power components. Ensure that heat-sensitive areas are managed properly to prevent overheating.
- Mechanical Strength: Reinforce critical areas of the PCB to avoid flexing and damage during handling. Use ribbing or other structural enhancements to increase mechanical strength without significantly adding to thickness.
- 7. Signal Integrity: Maintain proper impedance control and minimize signal interference by following good routing practices. Ensure that high-speed signals have proper grounding and shielding.
- Manufacturing Tolerances: Design with the manufacturing process in mind. Ultra-thin PCBs are more sensitive to fabrication tolerances, so specify clear tolerances for dimensions and alignment to ensure compatibility with manufacturing capabilities.
- Testing and Quality Control: Implement robust testing methods to verify the board’s functionality and reliability. Perform thorough inspections to catch defects that might arise due to the thin profile and delicate construction.
- Assembly Considerations: Choose appropriate soldering and assembly techniques suitable for ultra-thin PCBs. Ensure that the assembly process does not damage the board due to its thin nature.
By adhering to these design guidelines, you can effectively manage the challenges of ultra-thin hard PCBs and achieve a reliable, high-performance circuit board suitable for advanced applications.
What is the Ultra Thin Hard PCB Fabrication Process?
The fabrication process for ultra-thin hard PCBs involves several specialized steps to achieve the desired thin profile while maintaining high performance and reliability. Here’s a detailed look at the process:
- Material Preparation:Select and prepare high-quality, thin core materials, such as epoxy resin or FR-4 with reduced thickness. The core material must be stable and have suitable electrical and thermal properties.
- Laminate Layering: Apply copper foil to both sides of the core material. For multi-layer boards, additional layers of dielectric and copper are laminated together. This process uses heat and pressure to bond layers into a single, thin laminate.
- Patterning: Transfer the circuit design onto the copper layers using photolithography. This involves applying a photosensitive coating, exposing it to UV light through a mask to define the circuit patterns, and then developing the exposed areas to reveal the copper traces.
- Etching: Remove unwanted copper from the board using an etching solution. This step creates the circuit traces and pads by dissolving the exposed copper areas while leaving the desired circuit pattern intact.
- Drilling: Drill holes for vias and component leads using precision laser drilling or mechanical drilling. For ultra-thin PCBs, this step requires high accuracy to avoid damaging the delicate substrate.
- Plating: Plate the drilled holes with copper to form electrical connections between layers. This step involves a chemical deposition process to coat the interior walls of the holes with a thin layer of copper.
- Electrical Testing:Perform electrical tests to check for shorts, opens, and other defects in the circuit. Testing ensures that the PCB meets design specifications before proceeding to the next steps.
- Overlay and Solder Mask:Apply a solder mask layer to protect the copper traces and prevent solder bridging during assembly. The solder mask is typically a thin layer of epoxy resin or polymer applied over the board and cured to a hardened state.
- Silkscreen Printing: Print identifying marks, component outlines, and other information onto the PCB using silkscreen ink. This step is essential for proper component placement and board identification.
- Cutting and Routing: Cut and route the PCB to its final dimensions using precision cutting techniques. For ultra-thin PCBs, ensure that the cutting process does not cause mechanical stress or damage to the thin substrate.
- Final Inspection and Testing: Conduct a final inspection to check for defects such as scratches, alignment issues, or incomplete etching. Perform additional electrical testing to ensure that the PCB functions correctly.
- Packaging: Once the PCB passes all quality checks, it is packaged for shipping. Proper packaging is crucial to prevent damage during transportation, especially given the delicate nature of ultra-thin boards.
By following these steps, manufacturers can produce high-quality ultra-thin hard PCBs that meet stringent design and performance criteria while maintaining the thin profile necessary for modern electronic applications.
How do you Manufacture an Ultra Thin Hard PCB?
Manufacturing an ultra-thin hard PCB involves several precise and advanced techniques to achieve a thin, rigid circuit board with high reliability. Here’s a step-by-step overview of the process:
- Material Selection: Choose high-quality base materials that are thin and have good mechanical and electrical properties. Common choices include low-thickness epoxy resin or advanced composites. The material must withstand fabrication processes and meet performance requirements.
- Core Preparation: For multi-layer PCBs, prepare the core material by laminating thin layers of dielectric material with copper foil on both sides. The core should be uniform and free of defects to ensure a reliable final product.
- Lamination:Apply copper foil to both sides of the core material using a lamination press. This process uses heat and pressure to bond the copper foil to the dielectric core, creating a thin, rigid laminate.
- Photolithography: Transfer the circuit design onto the copper layers using photolithography. Apply a photosensitive coating (photoresist) to the copper, expose it to UV light through a photomask that defines the circuit pattern, and develop the exposed photoresist to reveal the copper traces.
- Etching: Remove unwanted copper using an etching solution, leaving behind the desired circuit pattern. This step is critical for defining the precise traces and pads on the ultra-thin PCB.
- Drilling:Use high-precision laser drilling or mechanical drilling to create vias and holes for component leads. Given the board’s thinness, careful control is necessary to avoid damaging the substrate.
- Plating:Plate the drilled holes with copper to form electrical connections between layers. This process involves depositing a thin layer of copper onto the walls of the vias through an electroplating process.
- Solder Mask Application: Apply a solder mask layer to protect the copper traces and pads from solder during assembly. The solder mask is typically a thin layer of epoxy or polymer that is cured to a hard, protective finish.
- Silkscreen Printing: Print identifying marks, component outlines, and other necessary information onto the PCB using silkscreen ink. This helps in component placement and provides visual guidance during assembly.
- Cutting and Routing: Cut and route the PCB to its final dimensions using precision cutting techniques. For ultra-thin PCBs, it is essential to handle the material carefully to prevent warping or damage.
- Final Testing and Inspection: Perform comprehensive testing to check for electrical and mechanical defects. This includes inspecting for shorts, opens, and verifying that the PCB meets all design specifications.
- Packaging: Package the finished PCBs carefully to prevent damage during transportation. Given the delicate nature of ultra-thin boards, use protective packaging materials to ensure the boards remain intact.
By meticulously following these steps, manufacturers can produce ultra-thin hard PCBs that meet high standards of performance and reliability, suitable for advanced electronic applications where space and weight constraints are critical.
How Much Should an Ultra Thin Hard PCB Cost?
The cost of an ultra-thin hard PCB can vary significantly based on several factors. Here’s a breakdown of key considerations that influence the pricing:
- Thickness and Complexity:The thinner the PCB, the more challenging it is to manufacture. Ultra-thin PCBs require precise handling and advanced technology, which can drive up costs. Complex designs with multiple layers or intricate patterns will also increase the price.
- Material Costs: High-quality materials used for ultra-thin PCBs, such as specialty epoxy resins or advanced composites, can be more expensive than standard materials. The cost of copper foil and other components also affects the overall price.
- Manufacturing Volume: Production volume plays a significant role in cost. Generally, higher volumes lead to lower per-unit costs due to economies of scale. Small batch or prototype runs will be more expensive per unit compared to large production runs.
- Layer Count: Multi-layer PCBs involve additional processes like lamination and drilling, which can increase the cost. Reducing the number of layers can help lower the cost but may impact functionality and design flexibility.
- Precision and Tolerances: Ultra-thin PCBs require high precision and tighter tolerances, which necessitates advanced manufacturing equipment and quality control measures. This added precision can increase manufacturing costs.
- Additional Features: Special features such as gold plating, special solder masks, or unique surface finishes will contribute to higher costs. Customization options also affect the final price.
- Testing and Inspection: Comprehensive testing and quality assurance processes are crucial for ultra-thin PCBs to ensure reliability and performance. The cost of these tests is factored into the overall price.
- Lead Time: Faster turnaround times may incur additional costs. Standard production schedules are generally less expensive than expedited manufacturing services.
Overall, the cost of an ultra-thin hard PCB can range from a few dollars per unit for high-volume production to several hundred dollars for custom prototypes or low-volume runs. It’s essential to discuss specific requirements with manufacturers to obtain an accurate quote tailored to the project’s needs.
What is Ultra Thin Hard PCB Base Material?
The base material for ultra-thin hard PCBs is crucial for ensuring the board’s performance and durability. Here’s a detailed overview of the materials commonly used for ultra-thin hard PCBs:
- Epoxy Resin:One of the most widely used base materials for ultra-thin PCBs. Epoxy resin offers good electrical insulation properties and can be formulated to achieve thin, rigid layers. It is often used in combination with fiberglass or other reinforcing materials to enhance mechanical strength.
- FR-4: A type of epoxy glass laminate, FR-4 is commonly used in standard PCBs but can also be adapted for ultra-thin applications. It provides good electrical insulation and mechanical stability, though special formulations and processes may be required to achieve ultra-thin profiles.
- Polyimide: Known for its high thermal stability and flexibility, polyimide is used in applications requiring extreme performance characteristics. It can be engineered to be very thin while maintaining excellent thermal and electrical properties. Polyimide-based PCBs are often used in high-temperature environments.
- High-Density Interconnect (HDI) Materials: These materials are designed for high-density, high-performance applications. They often include advanced dielectric materials that can be used to produce ultra-thin PCBs with high reliability and performance.
- Ceramic Materials: Some ultra-thin hard PCBs use ceramic materials due to their excellent thermal conductivity and electrical properties. Ceramic substrates are often used in specialized applications where high performance and heat dissipation are critical.
- Paper Phenolic: Although less common in ultra-thin designs due to its relative fragility and lower performance compared to other materials, paper phenolic can be used in applications where cost is a major factor and performance requirements are less stringent.
- Aluminum and Copper Core Materials: For specific applications, ultra-thin PCBs may use metal core materials to enhance thermal management. These cores are often combined with thin layers of dielectric material to achieve the desired thickness and performance.
By selecting the appropriate base material for the intended application, manufacturers can produce ultra-thin hard PCBs that meet the specific requirements for performance, durability, and functionality.
Which Company Makes Ultra Thin Hard PCBs?
Manufacturing ultra-thin hard PCBs (Printed Circuit Boards) requires high-precision technology and advanced manufacturing equipment. Here are some well-known companies that produce ultra-thin hard PCBs:
- TSMC (Taiwan Semiconductor Manufacturing Company):TSMC is not only a leading global semiconductor manufacturer but also involved in producing high-performance PCBs, including ultra-thin hard PCBs. These are mainly used in high-end electronic products such as smartphones and high-performance computing devices.
- Foxconn: As one of the world’s largest electronic contract manufacturers, Foxconn produces various types of PCBs, including ultra-thin hard PCBs. Their ultra-thin PCBs are primarily used in consumer electronics and communication devices.
- Greatek Electronics: Greatek Electronics specializes in high-tech PCB production, including ultra-thin hard PCBs. Their products are widely used in consumer electronics, communications, medical devices, and other fields.
- Shengyi Technology:Shengyi Technology is a global leader in PCB manufacturing, offering a variety of PCB solutions, including ultra-thin hard PCBs. Their products are known for their high quality and reliability, and are used across multiple industries.
- Nanya Technology: Nanya Technology, known for memory chips, also engages in PCB manufacturing, including ultra-thin hard PCBs. Their PCB products are mainly used in high-performance electronic devices.
Our Company’s Ultra-Thin Hard PCB Production Capabilities:
Our company is capable of producing ultra-thin hard PCBs, offering high-quality and high-performance solutions. Here are the features of our ultra-thin hard PCBs:
- Material Selection: We use high-quality base materials, such as specialty epoxy resins and polyimide, to ensure that the PCBs maintain excellent electrical performance and mechanical strength despite their thin profile.
- Precision Manufacturing: We employ advanced manufacturing processes, such as laser drilling and high-precision etching, to ensure the accuracy and reliability of ultra-thin PCBs. Our production equipment can handle extremely thin substrates, ensuring each PCB meets stringent design requirements.
- Quality Control: We implement strict quality control measures during the manufacturing process, including electrical testing, visual inspection, and performance verification. Each PCB undergoes comprehensive testing before leaving the factory to ensure stability and reliability in actual applications.
- Custom Services: We offer customization services based on specific customer needs, including varying thicknesses, layer counts, and feature requirements. Whether for prototype design or large-scale production, we provide flexible solutions.
- Industry Applications: Our ultra-thin hard PCBs are widely used in consumer electronics, communication devices, medical equipment, and other fields. We are committed to delivering high-quality, high-performance PCB solutions to meet demanding technical requirements.
By combining advanced technology and materials, our company is able to produce ultra-thin hard PCBs that meet the highest standards, providing exceptional products and services to our customers.
What are the 7 Qualities of Good Customer Service?
Good customer service is essential for building strong relationships with customers and ensuring their satisfaction. Here are seven key qualities that define excellent customer service:
- Responsiveness:Good customer service is characterized by prompt responses to customer inquiries and issues. Being quick to acknowledge and address customer needs shows that you value their time and are committed to resolving their problems efficiently.
- Empathy:Understanding and sharing the feelings of customers is crucial. Empathetic service involves actively listening to customers, recognizing their concerns, and responding in a way that shows genuine care and understanding. This helps in building a stronger connection and trust.
- Knowledgeability: Providing accurate and relevant information is vital. Customer service representatives should be well-trained and knowledgeable about the products or services offered, as well as company policies and procedures. This ensures they can effectively answer questions and resolve issues.
- Patience: Handling customer inquiries and complaints with patience is essential, especially in challenging situations. Taking the time to carefully address customer concerns without rushing them or becoming frustrated demonstrates respect and professionalism.
- Clear Communication: Effective communication involves conveying information clearly and concisely. This includes avoiding jargon, using simple language, and ensuring that customers understand the solutions or responses provided. Good communication helps prevent misunderstandings and ensures that customer needs are met accurately.
- Consistency:Providing a consistent level of service across different interactions and channels is crucial for maintaining customer trust. Consistency in service quality ensures that customers receive the same positive experience regardless of when or how they contact the company.
- Follow-Up: Good customer service involves following up with customers after resolving their issues or fulfilling their requests. This demonstrates a commitment to customer satisfaction and helps identify any remaining concerns or opportunities for improvement.
By embodying these qualities, companies can deliver exceptional customer service that not only meets but exceeds customer expectations, fostering loyalty and positive relationships.
FAQs
What is an ultra-thin hard PCB?
An ultra-thin hard PCB (Printed Circuit Board) is a type of PCB characterized by its exceptionally thin profile combined with rigid characteristics. It is designed to provide high performance and reliability in compact and space-constrained applications.
What are the typical applications for ultra-thin hard PCBs?
Ultra-thin hard PCBs are commonly used in high-density electronic devices where space is at a premium. Applications include smartphones, tablets, wearable electronics, medical devices, and high-performance computing equipment.
What materials are used in ultra-thin hard PCBs?
Common materials include specialty epoxy resins, polyimides, and advanced composites. These materials are selected for their excellent electrical insulation, mechanical strength, and thermal stability, even at reduced thicknesses.
How are ultra-thin hard PCBs manufactured?
The manufacturing process involves several steps: material selection, core preparation, lamination, photolithography, etching, drilling, plating, solder mask application, silkscreen printing, and cutting. Precision and advanced technology are critical to achieve the required thinness and reliability.
What are the design considerations for ultra-thin hard PCBs?
Design considerations include ensuring adequate mechanical support despite the thin profile, managing heat dissipation, maintaining electrical performance, and optimizing trace layout and spacing. Designers must also account for the increased difficulty in handling and processing ultra-thin materials.
How do ultra-thin hard PCBs compare to standard PCBs?
Ultra-thin hard PCBs differ from standard PCBs primarily in their thickness. They offer similar performance characteristics but are designed to be much thinner, which can affect factors like mechanical stability and thermal management. They are often used in applications where space is a critical constraint.
What are the challenges in manufacturing ultra-thin hard PCBs?
Challenges include handling and processing thin materials without damage, maintaining high precision in manufacturing processes, ensuring consistent quality control, and addressing potential issues with heat dissipation and mechanical strength.