Ultra-thin Hard PCB Manufacturer
Ultra-thin Hard PCB Manufacturer,Ultra-thin hard PCBs represent a cutting-edge innovation in electronic circuitry, boasting an extraordinary combination of slimness and resilience. These PCBs, engineered with meticulous precision, are designed to meet the demanding requirements of modern electronic devices where space optimization is paramount. Utilizing advanced materials such as fiberglass-reinforced epoxy laminate (FR-4) or polyimide, they maintain exceptional rigidity despite their incredibly thin profile, making them ideal for applications where weight reduction and compactness are crucial, such as in smartphones, wearables, and aerospace technologies. With their minimized thickness, ultra-thin hard PCBs not only enable sleeker device designs but also offer improved thermal performance and enhanced electrical properties, ensuring reliable and efficient operation. Their intricate design and manufacturing processes involve sophisticated techniques like microvia technology and precision drilling, resulting in high-performance circuitry capable of meeting the stringent demands of today’s technology-driven world. In essence, ultra-thin hard PCBs epitomize the fusion of cutting-edge engineering and innovation, driving forward the evolution of compact electronic devices.
What is an Ultra-thin hard PCB?
An Ultra-thin hard PCB (Printed Circuit Board) refers to a type of PCB that is exceptionally thin while still maintaining rigidity. These PCBs are designed for applications where space is at a premium and weight reduction is critical, such as in smartphones, tablets, wearables, and other portable electronic devices.
The term “hard” in this context typically implies that the PCB substrate is made of a rigid material like fiberglass-reinforced epoxy laminate. This rigidity ensures that the PCB maintains its shape and structural integrity even when it’s extremely thin.
Ultra-thin hard PCBs often have several layers of copper traces and insulating material sandwiched together. Advanced manufacturing techniques, such as laser drilling and microvia technology, are used to create intricate circuit patterns in these thin layers.
These PCBs require careful design and manufacturing processes to ensure they meet performance requirements while being thin enough to fit into tight spaces. They offer advantages such as reduced weight, improved thermal performance, and enhanced electrical performance due to shorter signal paths.
Overall, ultra-thin hard PCBs are crucial components in the development of compact and lightweight electronic devices.
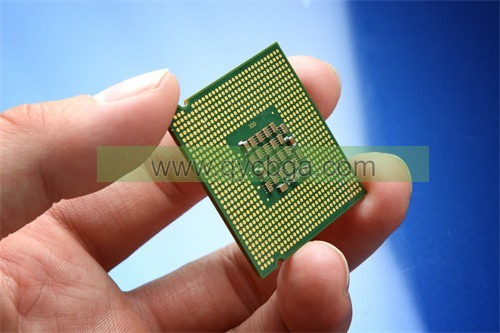
Ultra-thin Hard PCB Manufacturer
What are Ultra-thin hard PCB Design Guidelines?
Designing ultra-thin hard PCBs requires careful consideration of various factors to ensure the functionality, reliability, and manufacturability of the board. Here are some design guidelines:
- Material Selection: Choose a high-quality, rigid substrate material suitable for ultra-thin applications, such as fiberglass-reinforced epoxy laminate (FR-4) or similar materials.
- Thickness: Determine the desired thickness of the PCB, balancing the need for thinness with structural integrity and manufacturability. Typical thicknesses for ultra-thin PCBs range from 0.2mm to 0.8mm.
- Layer Stackup: Optimize the layer stackup to minimize thickness while meeting performance requirements. Consider using microvia technology to enable more complex designs with reduced layer count.
- Trace Width and Spacing: Use appropriate trace widths and spacing to accommodate the desired current-carrying capacity and impedance requirements while ensuring manufacturability. Thinner traces may be necessary in ultra-thin designs, but be mindful of signal integrity and reliability.
- Component Placement: Place components strategically to minimize board size and optimize signal paths. Consider the height of components and ensure clearance for assembly processes.
- Thermal Management: Implement thermal relief pads for components connected to power or generating heat to facilitate efficient heat dissipation. Consider adding thermal vias to improve heat transfer to internal layers or heat sinks.
- Mechanical Support: Reinforce the PCB with additional support structures or stiffeners if necessary to prevent flexing or warping, especially in applications with mechanical stress.
- Manufacturability: Design the PCB with manufacturability in mind, considering the capabilities and limitations of the chosen fabrication processes. Avoid features that may be challenging to manufacture, such as extremely thin traces or tight spacing between pads.
- Signal Integrity: Minimize signal distortion and interference by carefully routing high-speed signal traces, maintaining controlled impedance, and reducing crosstalk between traces.
- Testing and Validation: Perform thorough testing and validation of the design to ensure functionality, reliability, and compliance with specifications. Consider simulating the PCB’s performance using electronic design automation (EDA) tools.
By following these guidelines, designers can create ultra-thin hard PCBs that meet the stringent requirements of modern electronic devices while optimizing performance and manufacturability.
What is the Ultra-thin hard PCB Fabrication Process?
The fabrication process for ultra-thin hard PCBs is similar to that of standard PCBs but requires special attention to detail due to the thinness of the board. Here’s an overview of the typical fabrication process:
- Design: The process begins with the PCB design, where the circuit schematic is translated into a layout using PCB design software. Designers consider factors such as component placement, trace routing, layer stackup, and mechanical constraints.
- Material Selection: Choose a high-quality, rigid substrate material suitable for ultra-thin applications, such as fiberglass-reinforced epoxy laminate (FR-4) or similar materials. The material should be thin yet durable enough to maintain structural integrity.
- Preparation of Substrate:The chosen substrate material is prepared by cutting it to the desired size and cleaning it thoroughly to remove any contaminants that could affect the bonding of copper and other materials.
- Copper Cladding: A thin layer of copper foil is laminated onto the substrate material using heat and pressure. This copper foil serves as the conductive layer for the PCB.
- Layer Alignment and Bonding: If the PCB design requires multiple layers, the layers are aligned and bonded together using heat and pressure. This process may involve the use of adhesives or pre-pregs (pre-impregnated resin systems).
- Drilling: Holes are drilled into the PCB for through-hole components, vias, and mounting holes. Specialized drilling techniques may be used to achieve precise hole sizes and locations.
- Copper Etching: The unwanted copper is etched away using chemical processes, leaving behind the desired copper traces and pads according to the PCB design.
- Surface Finishing: Surface finishing processes such as solder mask application and copper plating are performed to protect the copper traces, provide insulation between conductive elements, and improve solderability.
- Silkscreen Printing: Information such as component labels, reference designators, and logos are printed onto the PCB surface using silkscreen printing techniques.
- Testing: The fabricated PCB undergoes various tests to ensure functionality, reliability, and compliance with specifications. This may include electrical testing, visual inspection, and automated optical inspection (AOI).
- Panelization and Routing: If multiple PCBs are fabricated simultaneously on a larger panel, they are separated (routed) from the panel after fabrication.
- Final Inspection and Packaging: The finished PCBs undergo a final inspection to check for any defects or irregularities. Once approved, they are packaged and prepared for shipment to the customer or assembly facility.
Throughout the fabrication process, strict quality control measures are implemented to ensure that the ultra-thin hard PCBs meet the required specifications and standards. Advanced manufacturing techniques and equipment may be employed to handle the challenges associated with thin substrates and fine features.
How do you manufacture an Ultra-thin hard PCB?
Manufacturing an ultra-thin hard PCB involves several specialized processes to ensure the final product meets the desired thickness, rigidity, and performance criteria. Here’s a step-by-step overview of the manufacturing process:
- Design Preparation: The manufacturing process begins with the design of the PCB. Designers use CAD (Computer-Aided Design) software to create the layout, considering factors such as component placement, trace routing, layer stackup, and mechanical constraints. Special attention is given to minimizing the thickness of the PCB while maintaining structural integrity.
- Material Selection: Choose a high-quality substrate material suitable for ultra-thin applications, such as fiberglass-reinforced epoxy laminate (FR-4) or similar materials. The material should have the necessary rigidity to support the thin design while still being lightweight.
- Substrate Preparation: The substrate material is prepared by cutting it to the desired size and cleaning it thoroughly to remove any contaminants that could affect adhesion or conductivity.
- Copper Cladding: A thin layer of copper foil is laminated onto the substrate material using heat and pressure. This copper foil serves as the conductive layer for the PCB. The thickness of the copper foil is carefully controlled to meet the design specifications.
- Layer Alignment and Bonding:If the PCB design requires multiple layers, the layers are aligned and bonded together using heat and pressure. This process may involve the use of adhesives or pre-pregs (pre-impregnated resin systems) to ensure proper bonding between the layers.
- Drilling: Holes are drilled into the PCB for through-hole components, vias, and mounting holes. Specialized drilling techniques may be used to achieve precise hole sizes and locations, taking into account the thinness of the PCB.
- Copper Etching: The unwanted copper is etched away using chemical processes, leaving behind the desired copper traces and pads according to the PCB design. Etching is carefully controlled to ensure the integrity of the thin traces.
- Surface Finishing: Surface finishing processes such as solder mask application and copper plating are performed to protect the copper traces, provide insulation between conductive elements, and improve solderability. These processes are adapted to accommodate the thinness of the PCB.
- Silkscreen Printing: Information such as component labels, reference designators, and logos are printed onto the PCB surface using silkscreen printing techniques. Care is taken to ensure that the printing does not add significant thickness to the PCB.
- Testing: The fabricated PCB undergoes various tests to ensure functionality, reliability, and compliance with specifications. This may include electrical testing, visual inspection, and automated optical inspection (AOI) to detect any defects or irregularities.
- Panelization and Routing: If multiple PCBs are fabricated simultaneously on a larger panel, they are separated (routed) from the panel after fabrication. This step may involve specialized equipment to handle the thin and fragile PCBs.
- Final Inspection and Packaging: The finished PCBs undergo a final inspection to verify quality and adherence to specifications. Once approved, they are packaged and prepared for shipment to the customer or assembly facility.
Throughout the manufacturing process, strict quality control measures are implemented to ensure that the ultra-thin hard PCBs meet the required specifications and standards. Advanced manufacturing techniques and equipment may be employed to handle the challenges associated with thin substrates and fine features.
How much should an Ultra-thin hard PCB cost?
The cost of an ultra-thin hard PCB can vary significantly depending on several factors, including:
- Size and Complexity: Larger and more complex PCBs with dense circuitry will generally cost more to manufacture due to increased material usage and production time.
- Material: The choice of substrate material and copper thickness can influence the cost. High-quality materials and thinner copper foils may come at a higher price.
- Layer Count: PCBs with multiple layers require more manufacturing steps and materials, resulting in higher costs compared to single-layer or double-layer boards.
- Technology and Features: Advanced technologies such as microvia drilling, impedance control, and high-speed signal routing can increase manufacturing costs due to specialized equipment and expertise required.
- Surface Finish and Features: The type of surface finish (e.g., ENIG, HASL, OSP) and additional features like gold plating or edge connectors can impact the overall cost.
- Quantity: Economies of scale often apply in PCB manufacturing, with higher quantities leading to lower per-unit costs. However, initial setup costs for small production runs may offset these savings.
- Turnaround Time: Expedited or rush orders may incur additional charges to prioritize production and meet tight deadlines.
- Supplier and Location: PCB fabrication costs can vary between suppliers and regions due to differences in labor costs, overhead expenses, and manufacturing capabilities.
As a rough estimate, the cost of an ultra-thin hard PCB can range from a few dollars for simple prototypes to several hundred dollars or more for complex, high-performance boards in large quantities. It’s essential to obtain quotes from multiple PCB manufacturers and consider the specific requirements of your project to determine an accurate cost. Additionally, factors like quality, reliability, and technical support should also be considered alongside price when choosing a PCB supplier.
What is Ultra-thin hard PCB base material?
The base material for ultra-thin hard PCBs typically consists of rigid substrates that provide structural support while maintaining a thin profile. Common materials used for ultra-thin hard PCBs include:
- Fiberglass-Reinforced Epoxy Laminate (FR-4): FR-4 is the most widely used material for PCB substrates due to its excellent electrical insulation properties, mechanical strength, and affordability. It consists of layers of woven fiberglass impregnated with epoxy resin.
- Polyimide (PI): Polyimide is a high-performance polymer known for its exceptional thermal stability, flexibility, and resistance to chemicals. It is commonly used in applications requiring ultra-thin and flexible PCBs, such as in aerospace, automotive, and medical devices.
- Rogers RO4000 Series: Rogers Corporation produces high-frequency laminates specifically designed for RF/microwave applications. These laminates offer excellent electrical performance, low dielectric loss, and stability over a wide range of frequencies. Some variants within the RO4000 series are suitable for ultra-thin PCBs.
- Aluminum: Aluminum-based PCBs are used in applications where lightweight and high thermal conductivity are essential, such as in LED lighting and automotive electronics. Aluminum-based substrates can be manufactured to ultra-thin specifications while providing good rigidity.
- Ceramic: Ceramic substrates offer excellent thermal properties, high mechanical strength, and superior electrical insulation. They are often used in high-power and high-frequency applications where heat dissipation and reliability are critical.
These materials can be manufactured to ultra-thin dimensions while still providing the necessary rigidity and electrical properties required for PCBs. The choice of base material depends on factors such as the application requirements, desired performance characteristics, and cost considerations.
Which company makes Ultra-thin hard PCB?
There are many companies specialized in producing ultra-thin hard PCBs, including Hitachi Chemical in Japan, Samsung Electronics in South Korea, Rogers Corporation in the United States, and Shenzhen Zhongzheng Circuit Technology Co., Ltd. in China. These companies have advanced manufacturing technologies and equipment to meet various demands for ultra-thin hard PCBs.
Our company is also a professional PCB manufacturer with rich experience and advanced production equipment. Our factory is equipped with the latest PCB manufacturing technology, including advanced thin film coating, precision drilling, precise cutting, and surface treatment equipment. Our team consists of experienced engineers and technical personnel who can provide customized solutions and technical support to customers.
We can produce ultra-thin hard PCBs with various specifications and thicknesses to meet specific customer requirements. Our PCB products have excellent electrical performance, stable structure, and reliable quality, suitable for various application fields, including consumer electronics, communication equipment, medical devices, and industrial control.
As a professional PCB manufacturer, we are committed to providing customers with high-quality products and excellent services. We will continue to invest in technological innovation and quality control to meet the growing demands of customers and establish long-term stable cooperation. Please feel free to contact us for more information about our company and our capabilities in manufacturing ultra-thin hard PCBs.
What are the 7 qualities of good customer service?
Good customer service is characterized by several key qualities that help build positive relationships with customers and ensure their satisfaction. Here are seven qualities of good customer service:
- Responsiveness: Good customer service involves being responsive to customers’ inquiries, concerns, and needs in a timely manner. This includes promptly answering phone calls, responding to emails, and addressing customer queries on social media platforms. A quick response demonstrates that the company values the customer’s time and is committed to resolving their issues promptly.
- Empathy: Empathy is the ability to understand and share the feelings of another person. Good customer service representatives demonstrate empathy by actively listening to customers, acknowledging their concerns, and showing genuine concern for their well-being. Empathetic interactions help customers feel understood and valued, fostering trust and loyalty.
- Professionalism: Professionalism encompasses a range of behaviors, including courtesy, respect, and competence. Good customer service representatives maintain a professional demeanor at all times, regardless of the customer’s behavior or the nature of the inquiry. They communicate clearly and effectively, provide accurate information, and handle challenging situations with grace and composure.
- Problem-solving skills: Good customer service involves effectively resolving customer issues and concerns to their satisfaction. This requires strong problem-solving skills, including the ability to analyze situations, identify root causes, and propose appropriate solutions. Customer service representatives should be proactive in addressing problems and finding creative ways to exceed customer expectations.
- Flexibility: Flexibility is essential in adapting to the diverse needs and preferences of customers. Good customer service representatives are flexible in their approach, willing to accommodate special requests, and able to tailor solutions to meet individual customer needs. They understand that every customer is unique and strive to provide personalized assistance accordingly.
- Consistency: Consistency is key to delivering a positive customer experience across all interactions and touchpoints. Good customer service is consistent in its quality, reliability, and adherence to company policies and standards. Customers should receive the same level of service whether they interact with the company online, over the phone, or in person.
- Follow-up: Follow-up is an important aspect of good customer service that demonstrates ongoing commitment to customer satisfaction. After resolving a customer’s issue or fulfilling a request, good customer service representatives follow up to ensure that the customer is satisfied with the outcome. They may also proactively reach out to customers to gather feedback, address any remaining concerns, or offer additional assistance.
By embodying these qualities, companies can cultivate strong relationships with customers, enhance brand reputation, and drive long-term success.Going above and beyond
FAQs
What is an ultra-thin hard PCB?
An ultra-thin hard PCB is a type of printed circuit board that is exceptionally thin while maintaining rigidity. It is designed for applications where space and weight reduction are critical, such as in smartphones, wearables, and other compact electronic devices.
What are the advantages of ultra-thin hard PCBs?
Ultra-thin hard PCBs offer advantages such as reduced weight, improved thermal performance, enhanced electrical performance due to shorter signal paths, and the ability to fit into tight spaces within electronic devices.
What materials are used in the fabrication of ultra-thin hard PCBs?
Common materials used in the fabrication of ultra-thin hard PCBs include fiberglass-reinforced epoxy laminate (FR-4), polyimide (PI), Rogers RO4000 series laminates, aluminum, and ceramic. These materials provide structural support while maintaining a thin profile.
What are the design considerations for ultra-thin hard PCBs?
Design considerations for ultra-thin hard PCBs include material selection, thickness optimization, trace width and spacing, component placement, thermal management, mechanical support, manufacturability, signal integrity, testing, and validation.
What are the fabrication processes involved in manufacturing ultra-thin hard PCBs?
The fabrication process for ultra-thin hard PCBs involves steps such as design preparation, material selection, substrate preparation, copper cladding, layer alignment and bonding, drilling, copper etching, surface finishing, silkscreen printing, testing, panelization, routing, final inspection, and packaging.
How much do ultra-thin hard PCBs cost?
The cost of ultra-thin hard PCBs can vary depending on factors such as size, complexity, material, layer count, technology, features, quantity, turnaround time, supplier, and location. Generally, costs range from a few dollars for prototypes to several hundred dollars or more for complex boards in large quantities.
Which companies manufacture ultra-thin hard PCBs?
Several companies specialize in the manufacture of ultra-thin hard PCBs, including Hitachi Chemical, Samsung Electronics, Rogers Corporation, and various PCB manufacturers worldwide.