Showa Denko MCL-E-770G Package Substrate Manufacturer
Showa Denko MCL-E-770G Package Substrate Manufacturer,Showa Denko MCL-E-770G package substrates represent cutting-edge technology in semiconductor packaging. Engineered with precision and expertise by Showa Denko K.K., these substrates offer exceptional performance and reliability for a wide range of semiconductor applications.
With advanced thermal management capabilities, the MCL-E-770G substrates effectively dissipate heat generated by semiconductor devices, ensuring optimal operating conditions and prolonging component lifespan. Their superior electrical properties, including low signal loss and high conductivity, enable seamless transmission of signals across the substrate, supporting the high-speed and high-frequency requirements of modern semiconductor devices.
Designed with versatility in mind, MCL-E-770G substrates are compatible with various packaging technologies, including flip-chip, wire-bond, and ball grid array (BGA) configurations. This versatility makes them suitable for diverse applications such as microprocessors, memory modules, graphic processors, and more.
Backed by stringent quality control measures and extensive testing protocols, Showa Denko ensures that every MCL-E-770G substrate meets the highest standards of performance and reliability. Whether in demanding industrial environments or consumer electronics, Showa Denko MCL-E-770G package substrates deliver unmatched quality and innovation, empowering next-generation semiconductor devices.
What is a Showa Denko MCL-E-770G package substrate?
The Showa Denko MCL-E-770G package substrate is a type of substrate used in semiconductor packaging. It’s manufactured by Showa Denko K.K., a Japanese chemical company. Package substrates serve as the foundation for mounting and interconnecting semiconductor devices such as integrated circuits (ICs) or chips.
The MCL-E-770G package substrate likely has specific characteristics such as high thermal conductivity, excellent electrical properties, and mechanical strength to ensure reliable performance of the semiconductor devices it supports. Additionally, it might have features tailored for specific applications or packaging technologies, such as flip-chip packaging or ball grid array (BGA) packaging.
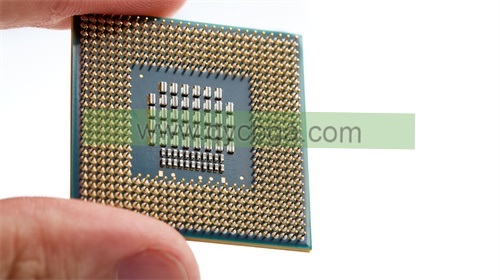
Showa Denko MCL-E-770G Package Substrate Manufacturer
What are the Showa Denko MCL-E-770G package substrate Design Guidelines?
Specific design guidelines for the Showa Denko MCL-E-770G package substrate might not be publicly available as they could be proprietary information held by Showa Denko K.K. or provided to customers under non-disclosure agreements. However, typical design guidelines for package substrates like the MCL-E-770G may include considerations such as:
- Material Properties: Understanding the thermal, mechanical, and electrical properties of the substrate material, including thermal conductivity, coefficient of thermal expansion (CTE), dielectric constant, and thickness.
- Layout and Routing: Guidelines for routing signal traces, power, and ground planes to minimize signal integrity issues such as crosstalk and impedance mismatch. This includes considerations for via placement, trace width and spacing, and signal termination.
- Power Delivery:Ensuring adequate power delivery to the semiconductor devices by optimizing power and ground plane layouts, minimizing voltage drops, and reducing loop inductance.
- Thermal Management: Designing effective heat dissipation solutions to manage the thermal performance of the substrate, such as thermal vias, heat sinks, or thermal pads.
- Package Compatibility: Ensuring compatibility with the specific semiconductor package type (e.g., flip-chip, wire-bond, BGA) and any associated assembly processes.
- Reliability and Durability: Designing for reliability under various operating conditions, including thermal cycling, mechanical stress, and humidity exposure.
- Signal Integrity: Minimizing signal degradation due to reflections, transmission line effects, and electromagnetic interference (EMI) by following best practices for high-speed signal routing and termination.
- Manufacturability: Designing for manufacturability to ensure that the substrate can be fabricated with high yield and consistency, considering factors such as process capabilities, tolerances, and assembly requirements.
These guidelines may vary depending on the specific application, package type, and performance requirements of the semiconductor device. Designers typically work closely with substrate manufacturers and utilize simulation tools to optimize the design for performance, reliability, and cost-effectiveness.
What is the Showa Denko MCL-E-770G package substrate Fabrication Process?
The specific fabrication process for the Showa Denko MCL-E-770G package substrate is proprietary information and may not be publicly disclosed by Showa Denko K.K. However, I can outline a general fabrication process for package substrates like the MCL-E-770G:
- Substrate Preparation: The process starts with preparing the substrate material, which could be a high-performance laminate composed of various layers of dielectric material, copper foils, and possibly other additives to enhance thermal or mechanical properties.
- Copper Foil Lamination:Copper foils are bonded to both sides of the substrate material using heat and pressure. These copper foils serve as the conductive layers for routing signals, power, and ground connections.
- Laser Drilling: Holes or vias are drilled into the substrate using laser technology. These vias serve as electrical connections between different layers of the substrate and facilitate interconnection between semiconductor devices mounted on the substrate.
- Circuit Patterning: A layer of photoresist is applied to the copper foils, which is then exposed to UV light through a photomask to define the desired circuit patterns. After exposure, the photoresist is developed, leaving behind the desired copper traces and pads.
- Etching: Exposed copper areas not protected by the developed photoresist are chemically etched away, leaving behind the circuit traces and pads.
- Surface Finish: The exposed copper surfaces are typically treated with a surface finish to improve solderability and prevent oxidation. Common surface finishes include immersion tin, immersion silver, electroless nickel immersion gold (ENIG), or organic solderability preservatives (OSP).
- Quality Control: Throughout the fabrication process, various quality control measures are implemented to ensure that the substrate meets the specified dimensional tolerances, electrical properties, and reliability requirements.
- Testing and Inspection: Finished substrates undergo rigorous testing and inspection to verify electrical continuity, insulation resistance, thermal performance, and other critical parameters.
- Packaging and Shipping: Once the substrates pass inspection, they are packaged and shipped to semiconductor assembly facilities for the mounting of semiconductor devices.
It’s important to note that the actual fabrication process may vary depending on factors such as substrate material, design complexity, and manufacturing capabilities. Additionally, proprietary technologies and process optimizations may be implemented by manufacturers like Showa Denko K.K. to differentiate their products in the market.
How do you manufacture a Showa Denko MCL-E-770G package substrate?
Manufacturing a Showa Denko MCL-E-770G package substrate involves a series of steps that require precision equipment, controlled environments, and expertise in materials science and semiconductor packaging. While the specific details of the process are proprietary to Showa Denko K.K., I can provide an overview of the typical steps involved:
- Substrate Material Selection: The process begins with selecting high-quality substrate materials that meet the desired electrical, thermal, and mechanical specifications. These materials may include laminates composed of dielectric layers and copper foils.
- Preparation and Cleaning: The substrate materials are prepared by cutting them to the required size and cleaning them to remove any contaminants that could affect the manufacturing process or the performance of the final product.
- Copper Foil Lamination:Copper foils are bonded to both sides of the substrate material using heat and pressure. This creates a conductive layer that will serve as the foundation for routing electrical connections on the substrate.
- Drilling and Via Formation: Precision drilling techniques, such as laser drilling, are used to create holes or vias in the substrate. These vias will later facilitate the interconnection of semiconductor devices mounted on the substrate.
- Circuit Patterning: A layer of photoresist is applied to the copper foils, which is then exposed to UV light through a photomask to define the desired circuit patterns. After exposure, the photoresist is developed, leaving behind the desired copper traces and pads.
- Etching:Chemical etching processes are used to selectively remove the exposed copper areas not protected by the developed photoresist. This defines the final circuit traces and pads on the substrate.
- Surface Finish: The exposed copper surfaces are treated with a surface finish to improve solderability and prevent oxidation. Common surface finishes include immersion tin, immersion silver, electroless nickel immersion gold (ENIG), or organic solderability preservatives (OSP).
- Quality Control and Testing: Throughout the manufacturing process, various quality control measures are implemented to ensure that the substrate meets the specified dimensional tolerances, electrical properties, and reliability requirements. Finished substrates undergo rigorous testing and inspection before being released for further processing.
- Packaging and Shipping: Once the substrates pass inspection, they are packaged and shipped to semiconductor assembly facilities for the mounting of semiconductor devices.
This manufacturing process requires a combination of advanced equipment, skilled operators, and strict quality control procedures to produce high-performance package substrates like the Showa Denko MCL-E-770G. Additionally, continuous research and development efforts are likely undertaken to improve manufacturing efficiency, product performance, and reliability.
How much should a Showa Denko MCL-E-770G package substrate cost?
The cost of a Showa Denko MCL-E-770G package substrate can vary depending on several factors including:
- Size and Complexity: Larger substrates with more complex designs typically cost more due to increased material and manufacturing expenses.
- Material Composition: The specific materials used in the substrate, such as high-performance laminates and advanced surface finishes, can impact the cost.
- Quantity: Bulk orders may receive volume discounts, while smaller orders may incur higher unit costs.
- Customization: If the substrate requires customization or specialized features tailored to a specific application, this can increase the cost.
- Supplier Relationship: Established relationships with the manufacturer or distributor may result in more favorable pricing terms.
- Market Conditions: Fluctuations in raw material prices, supply chain disruptions, and market demand can all influence the overall cost.
What is the Showa Denko MCL-E-770G package substrate base material?
The base material of the Showa Denko MCL-E-770G package substrate is likely a specialized composite laminate designed specifically for semiconductor packaging applications. While the exact composition and formulation are proprietary to Showa Denko K.K., I can provide insights into the typical characteristics and components of such materials:
- Dielectric Layer: The substrate base material usually consists of multiple layers of dielectric material. These dielectric layers provide insulation between conductive traces and help to maintain signal integrity by minimizing crosstalk and interference. The dielectric material is carefully selected for its electrical properties, such as low loss tangent and consistent dielectric constant over a wide frequency range.
- Reinforcement: To enhance mechanical strength and dimensional stability, the base material may incorporate reinforcement materials such as woven glass fiber or non-woven aramid fiber. These reinforcements help prevent warpage and delamination during the manufacturing process and throughout the lifetime of the substrate.
- Copper Foils: Copper foils are typically bonded to both sides of the substrate to serve as the conductive layers for routing electrical connections. The copper foils are chosen for their high conductivity and compatibility with the substrate manufacturing process.
- Thermal Management Additives: Depending on the application requirements, the base material may include additives to enhance thermal conductivity and heat dissipation. These additives may include fillers such as ceramics, metals, or carbon nanotubes dispersed within the dielectric matrix.
- Adhesive Layers: Adhesive layers are used to bond the various components of the substrate together during the lamination process. These adhesive materials are selected for their compatibility with the substrate materials and their ability to provide strong and reliable bonding.
- Surface Finishes:The surface of the substrate may be treated with various finishes to improve solderability and prevent oxidation. Common surface finishes include immersion tin, immersion silver, electroless nickel immersion gold (ENIG), or organic solderability preservatives (OSP).
Overall, the base material of the Showa Denko MCL-E-770G package substrate is engineered to provide a balance of electrical performance, mechanical reliability, thermal management, and manufacturability required for advanced semiconductor packaging applications. Showa Denko K.K. likely conducts extensive research and development to optimize the formulation of the base material to meet the demanding requirements of their customers in the semiconductor industry.
Which company manufactures Showa Denko MCL-E-770G package substrates?
The Showa Denko MCL-E-770G package substrates are manufactured by Showa Denko K.K., a company based in Japan. Our company can produce similar package substrates with high performance and reliability to meet the demands of customers in semiconductor packaging. We have advanced manufacturing equipment and technology, as well as an experienced team of engineers, capable of customizing package substrates according to customers’ specifications and requirements.
Our production process includes the following steps:
- Material selection: We choose high-quality substrate materials, including premium dielectric layers and conductive layers, to ensure the substrate possesses the required electrical, thermal, and mechanical properties.
- Production equipment:We are equipped with advanced production equipment, including laser drilling machines, etching equipment, laminators, etc., to ensure precise manufacturing processes.
- Process control: We employ strict process control measures to ensure that each package substrate meets customers’ specifications and requirements while maintaining product consistency and reliability.
- Quality inspection: We conduct rigorous quality inspections, including electrical testing, reliability testing, etc., to ensure that the products exhibit excellent performance and reliability before delivery to customers.
- Customer customization:We can customize the design and specifications of package substrates according to customers’ needs, providing personalized solutions to meet the requirements of different application scenarios.
In summary, our company has the capability to produce high-quality package substrates and is willing to collaborate with customers to advance and apply semiconductor packaging technology.
What are the 7 qualities of good customer service?
Good customer service is characterized by several key qualities that contribute to a positive experience for customers. Here are seven qualities:
- Responsiveness: Good customer service involves promptly addressing customer inquiries, concerns, and issues. Responding to customers in a timely manner shows that their needs are valued and helps build trust and satisfaction.
- Empathy: Empathy is the ability to understand and share the feelings of others. Good customer service representatives demonstrate empathy by listening attentively to customers, acknowledging their emotions, and showing genuine concern for their needs.
- Clear Communication: Effective communication is essential for providing good customer service. Clear, concise, and courteous communication helps customers understand information, instructions, and solutions, reducing misunderstandings and frustration.
- Knowledgeability: Customers expect to receive accurate and helpful information from customer service representatives. Knowledgeable representatives possess a thorough understanding of the products or services offered, as well as company policies and procedures, enabling them to address customer inquiries and resolve issues effectively.
- Professionalism: Professionalism encompasses aspects such as politeness, respectfulness, and maintaining a positive attitude, even in challenging situations. Demonstrating professionalism fosters trust and confidence in customers and reflects positively on the company.
- Problem-Solving Skills: Good customer service involves the ability to identify and solve customer problems efficiently. Customer service representatives should be equipped with problem-solving skills, creativity, and resourcefulness to address customer concerns and find satisfactory resolutions.
- Consistency: Consistency is key to delivering a consistently high level of customer service across all interactions and touchpoints. Customers should receive the same quality of service regardless of the channel they use to contact the company or the individual they interact with.
By prioritizing these qualities, businesses can enhance customer satisfaction, loyalty, and retention, ultimately contributing to long-term success and growth.
FAQs
What is Showa Denko MCL-E-770G package substrate?
Showa Denko MCL-E-770G is a type of package substrate manufactured by Showa Denko K.K., designed for use in semiconductor packaging. It provides a foundation for mounting and interconnecting semiconductor devices.
What are the key features of MCL-E-770G package substrates?
The MCL-E-770G package substrate likely features high thermal conductivity, excellent electrical properties, and mechanical strength. It may also have specific characteristics tailored for advanced semiconductor packaging applications.
What are the advantages of using MCL-E-770G package substrates?
Advantages of using MCL-E-770G package substrates may include improved thermal management, enhanced electrical performance, reliability, and compatibility with various semiconductor packaging technologies.
What applications are suitable for MCL-E-770G package substrates?
MCL-E-770G package substrates are suitable for a wide range of semiconductor applications, including microprocessors, memory devices, graphic processors, and other integrated circuits (ICs) requiring high-performance packaging solutions.
What are the design guidelines for MCL-E-770G package substrates?
Design guidelines for MCL-E-770G package substrates may include considerations such as layout and routing, thermal management, signal integrity, manufacturability, and reliability. These guidelines ensure optimal performance and compatibility with semiconductor devices.
Where can I obtain MCL-E-770G package substrates?
MCL-E-770G package substrates are typically available through authorized distributors or directly from Showa Denko K.K. Customers can contact Showa Denko or their local distributors for pricing and availability information.
What are the manufacturing processes involved in producing MCL-E-770G package substrates?
The specific manufacturing processes for MCL-E-770G package substrates may include substrate preparation, copper foil lamination, laser drilling, circuit patterning, etching, surface finishing, quality control, and testing.