Ultrathin Antenna PCB Manufacturer
Ultrathin Antenna PCB Manufacturer,Ultrathin Antenna PCBs are specialized printed circuit boards designed to serve as antennas in wireless communication devices. Characterized by their thin and flexible construction, these PCBs offer a compact and space-saving solution for integrating antennas into modern electronic devices. By utilizing flexible substrate materials such as polyimide or liquid crystal polymer, Ultrathin Antenna PCBs can conform to the shape of the device housing, enabling seamless integration into smartphones, tablets, wearables, IoT devices, and more. Their low profile and lightweight design make them ideal for applications where space and weight constraints are critical considerations. Despite their thinness, Ultrathin Antenna PCBs maintain excellent electrical performance, providing reliable wireless connectivity across various frequency bands such as Wi-Fi, Bluetooth, cellular, and GPS. With their versatility, performance, and adaptability, Ultrathin Antenna PCBs play a vital role in enabling wireless communication in today’s interconnected world.
What is an Ultrathin Antenna PCB?
An Ultrathin Antenna PCB is a type of printed circuit board (PCB) that is specifically designed to function as an antenna for wireless communication devices. Unlike traditional antennas that may be bulky and rigid, ultrathin antenna PCBs are extremely thin and flexible, making them suitable for integration into small and compact electronic devices such as smartphones, tablets, wearables, and Internet of Things (IoT) devices.
These antennas are typically made using specialized materials and manufacturing techniques to achieve the required flexibility and performance. They can be designed to operate across various frequency bands, such as Wi-Fi, Bluetooth, cellular, GPS, and other wireless standards.
Ultrathin antenna PCBs offer several advantages, including:
- Compact Size:Their thin and flexible nature allows for easy integration into small and space-constrained devices.
- Low Profile:They have a minimal thickness, which is particularly advantageous for applications where space is limited.
- Durability:Despite being thin and flexible, these antennas are designed to withstand bending and other mechanical stresses encountered in everyday use.
- Customization:They can be tailored to meet the specific requirements of different wireless communication standards and device designs.
Overall, ultrathin antenna PCBs play a crucial role in enabling wireless connectivity in modern electronic devices while minimizing space and design constraints.
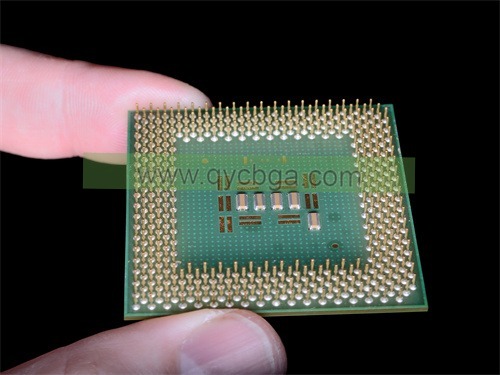
Ultrathin Antenna PCB Manufacturer
What are the Ultrathin Antenna PCB Design Guidelines?
Designing ultrathin antenna PCBs requires careful consideration of various factors to ensure optimal performance. Here are some guidelines typically followed in the design process:
- Substrate Selection:Choose a substrate material with low dielectric constant (εr) and loss tangent (tanδ) to minimize signal loss. Flexible substrates like polyimide are commonly used for ultrathin antenna PCBs due to their flexibility and low dielectric properties.
- Antenna Geometry:Select an appropriate antenna topology based on the application requirements and frequency bands of interest. Common types include monopole, dipole, patch, and inverted-F antennas. Ensure that the antenna geometry is compatible with the substrate material and fabrication process.
- Ground Plane Design:Design a solid ground plane beneath the antenna to enhance radiation efficiency and minimize interference. The ground plane should be as large as possible within the available space and should be kept continuous and free from discontinuities.
- Trace Width and Spacing:Determine the optimal trace width and spacing to achieve the desired impedance matching and radiation characteristics. Use wider traces for lower impedance and narrower traces for higher impedance. Maintain consistent trace widths and spacing to minimize signal distortion.
- Feedline Design:Design the feedline to match the impedance of the antenna and the transmission line. Use appropriate feeding techniques such as microstrip or stripline depending on the substrate type and fabrication process.
- Antenna Placement: Place the antenna away from other electronic components and metallic structures to minimize interference and detuning effects. Optimize the antenna placement for maximum radiation efficiency and coverage.
- Radiation Pattern Optimization:Simulate and optimize the antenna design using electromagnetic simulation software to achieve the desired radiation pattern, gain, and efficiency. Adjust the antenna geometry and dimensions as needed to meet the performance requirements.
- Flexibility Considerations:Ensure that the antenna design can withstand bending and flexing without significant degradation in performance. Use flexible substrate materials and incorporate mechanical features such as meanders or serpentine traces to enhance flexibility.
- Manufacturability:Consider the manufacturability of the antenna design, including fabrication processes such as etching, printing, and assembly. Choose fabrication techniques compatible with the selected substrate material and antenna geometry.
By following these design guidelines, engineers can develop ultrathin antenna PCBs that meet the performance, size, and flexibility requirements of various wireless communication applications.
What is the Ultrathin Antenna PCB Fabrication Process?
The fabrication process for ultrathin antenna PCBs involves several steps, including substrate preparation, antenna pattern formation, metallization, and assembly. Here’s an overview of the typical fabrication process:
- Substrate Selection:Choose a flexible substrate material suitable for the ultrathin antenna PCB. Common materials include polyimide (PI), liquid crystal polymer (LCP), and polyester (PET). The substrate should have low dielectric loss and mechanical flexibility.
- Substrate Cleaning:Clean the substrate surface thoroughly to remove any contaminants or residues that could affect the adhesion and quality of subsequent layers.
- Substrate Coating:Apply a thin layer of adhesive or release agent to the substrate surface to facilitate the bonding process and prevent sticking during fabrication.
- Antenna Pattern Formation:Use a photolithography or screen printing process to define the antenna pattern on the substrate. Photolithography involves depositing a photoresist layer on the substrate, exposing it to UV light through a mask with the desired pattern, and then developing the resist to reveal the antenna pattern. Alternatively, screen printing uses a stencil to apply conductive ink directly onto the substrate in the desired pattern.
- Metallization:Deposit a thin layer of conductive material onto the substrate to form the antenna traces and ground plane. Commonly used metals for ultrathin antenna PCBs include copper, silver, and gold. Metallization can be achieved through techniques such as sputtering, evaporation, or electroplating.
- Etching: Use chemical etching or laser ablation to selectively remove excess metal from the substrate, leaving behind the desired antenna pattern. Etching removes metal from areas not protected by the photoresist or stencil, defining the antenna traces and ground plane.
- Surface Finish:Apply a surface finish to the ultrathin antenna PCB to improve solderability and protect the conductive traces from oxidation. Common surface finishes include immersion tin, immersion silver, and gold plating.
- Assembly:If necessary, assemble additional components such as connectors, passive components, and integrated circuits onto the ultrathin antenna PCB using surface mount technology (SMT) or other assembly techniques.
- Testing and Quality Control:Perform electrical testing and inspection to verify the performance and quality of the ultrathin antenna PCB. Test parameters may include impedance matching, radiation efficiency, and signal integrity.
- Cutting and Packaging:Cut the ultrathin antenna PCB into the desired size and shape, and then package it for protection and integration into the final product.
By following these fabrication steps, manufacturers can produce ultrathin antenna PCBs with the required performance, flexibility, and reliability for a wide range of wireless communication applications.
How do you manufacture an Ultrathin Antenna PCB?
Manufacturing an ultrathin antenna PCB involves several steps, from designing the antenna to assembling the final product. Here’s a detailed overview of the manufacturing process:
- Design:Begin by designing the antenna PCB using specialized software. This involves selecting the antenna topology, determining the substrate material, designing the antenna geometry, feedline, and ground plane, and optimizing the layout for the desired performance.
- Substrate Preparation:Select a flexible substrate material such as polyimide (PI), liquid crystal polymer (LCP), or polyester (PET). Clean the substrate surface to remove any contaminants and ensure proper adhesion.
- Photolithography or Printing:Use photolithography or screen printing techniques to define the antenna pattern on the substrate. In photolithography, a photoresist layer is applied to the substrate, exposed to UV light through a mask with the desired pattern, and then developed to reveal the antenna pattern. Alternatively, screen printing applies conductive ink directly onto the substrate through a stencil.
- Metallization:Deposit a thin layer of conductive material onto the substrate to form the antenna traces and ground plane. Commonly used metals include copper, silver, and gold. Metallization can be achieved through techniques such as sputtering, evaporation, or electroplating.
- Etching:Use chemical etching or laser ablation to selectively remove excess metal from the substrate, leaving behind the desired antenna pattern. Etching removes metal from areas not protected by the photoresist or stencil, defining the antenna traces and ground plane.
- Surface Finish:Apply a surface finish to the antenna PCB to improve solderability and protect the conductive traces from oxidation. Common surface finishes include immersion tin, immersion silver, and gold plating.
- Assembly:If necessary, assemble additional components such as connectors, passive components, and integrated circuits onto the antenna PCB using surface mount technology (SMT) or other assembly techniques.
- Testing and Quality Control:Perform electrical testing and inspection to verify the performance and quality of the antenna PCB. Test parameters may include impedance matching, radiation efficiency, and signal integrity.
- Cutting and Packaging:Cut the antenna PCB into the desired size and shape, and then package it for protection and integration into the final product.
Throughout the manufacturing process, attention should be paid to maintaining precise dimensions, controlling material properties, and ensuring proper alignment of components to achieve the desired performance and reliability of the ultrathin antenna PCB.
How much should an Ultrathin Antenna PCB cost?
The cost of an ultrathin antenna PCB can vary widely depending on various factors such as the complexity of the design, materials used, manufacturing processes, quantity ordered, and supplier/vendor pricing. Here are some key factors that can influence the cost:
- Design Complexity:Intricate antenna designs with multiple layers, complex geometries, or specialized features may require more advanced fabrication techniques, resulting in higher manufacturing costs.
- Materials:The choice of substrate material, metallization method, and surface finish can impact the cost. High-performance materials such as liquid crystal polymer (LCP) may be more expensive than standard materials like polyimide (PI) or polyester (PET). Similarly, using precious metals like gold for metallization will increase the cost compared to copper or silver.
- Manufacturing Processes: Advanced manufacturing processes such as laser ablation, electroplating, or photolithography may incur higher costs due to equipment and labor expenses.
- Quantity:Generally, ordering larger quantities of ultrathin antenna PCBs can result in lower per-unit costs due to economies of scale. Suppliers may offer volume discounts for bulk orders.
- Lead Time:Expedited manufacturing and delivery options may come at an additional cost. Longer lead times typically result in lower overall costs.
- Quality and Reliability:Antenna PCBs designed and manufactured to meet stringent quality and reliability standards may command higher prices due to the additional testing and validation procedures involved.
- Supplier/Manufacturer:Different suppliers or manufacturers may offer varying pricing structures and levels of service. It’s essential to compare quotes from multiple vendors to ensure competitive pricing.
As a rough estimate, the cost of an ultrathin antenna PCB could range from a few dollars to several tens of dollars per unit for typical consumer electronics applications. For custom or high-performance applications, the cost could be higher. It’s advisable to consult with PCB manufacturers or suppliers for accurate cost estimates based on specific project requirements.
What is the Ultrathin Antenna PCB base material?
The base material for ultrathin antenna PCBs is typically a flexible substrate that provides mechanical flexibility while maintaining electrical performance. Common materials used for ultrathin antenna PCBs include:
- Polyimide (PI):PI is a popular choice for flexible PCBs due to its excellent thermal stability, mechanical flexibility, and low dielectric constant. It can withstand high temperatures encountered during fabrication processes such as soldering and assembly.
- Liquid Crystal Polymer (LCP):LCP is another commonly used material for ultrathin antenna PCBs. It offers high-frequency performance, low moisture absorption, and dimensional stability over a wide temperature range. LCP substrates are well-suited for applications requiring high-speed data transmission and miniaturization.
- Polyester (PET):PET is a cost-effective option for ultrathin antenna PCBs in applications where lower performance requirements or budget constraints are a consideration. While not as high-performing as PI or LCP, PET offers good flexibility and mechanical properties suitable for certain applications.
These base materials provide a foundation for the antenna PCB’s construction, allowing for the deposition of conductive traces, ground planes, and other necessary layers to create the antenna structure. The choice of base material depends on factors such as electrical performance requirements, mechanical flexibility, thermal properties, and cost considerations.
Which company makes Ultrathin Antenna PCBs?
There are many companies that manufacture Ultrathin Antenna PCBs, some of the well-known companies include Murata Manufacturing Co., Taoglas Limited, Fractus Antennas, and others. These companies have rich experience and technical expertise in the field of wireless communication and electronic devices, and they can provide various types and specifications of Ultrathin Antenna PCB products.
Our company is also one of the manufacturers of Ultrathin Antenna PCBs. As a company specializing in electronic device manufacturing, we have advanced production equipment and a skilled technical team, capable of providing high-quality Ultrathin Antenna PCB products. Our manufacturing process strictly adheres to international standards to ensure reliable product quality and excellent performance.
We can customize various types of Ultrathin Antenna PCBs according to the needs of customers, including different antenna topologies, frequency band coverage, and size specifications. Our products are suitable for various wireless communication applications, including smartphones, tablets, wearable devices, IoT devices, and more.
In addition to product quality and customization capabilities, we are also committed to providing high-quality customer service and technical support. Our team is dedicated to providing services such as technical consultation, sample production, and mass production support to meet the needs and expectations of customers.
In summary, our company has rich experience, advanced manufacturing technology, and excellent customer service, capable of meeting various customer requirements for Ultrathin Antenna PCBs. We look forward to cooperating with customers to promote the development and application of wireless communication technology.
What are the 7 qualities of good customer service?
Good customer service is essential for building strong relationships with customers and ensuring their satisfaction. Here are seven qualities of good customer service:
- Empathy:Good customer service representatives demonstrate empathy by understanding and acknowledging the customer’s feelings, concerns, and needs. They listen actively, show genuine concern, and strive to put themselves in the customer’s shoes to provide appropriate support.
- Patience:Patience is crucial in customer service, especially when dealing with challenging situations or customers who may be frustrated or upset. Good customer service representatives remain calm, composed, and attentive, even in difficult circumstances, and take the time to address the customer’s issues effectively.
- Communication Skills:Effective communication is key to providing good customer service. Customer service representatives should communicate clearly, concisely, and politely, using language that is easy to understand and respectful. They should also be good listeners, asking clarifying questions and providing relevant information to assist the customer.
- Problem-Solving Ability:Good customer service representatives are adept at problem-solving, finding solutions to customer issues promptly and efficiently. They analyze the situation, identify the root cause of the problem, and offer practical solutions or alternatives to resolve the issue to the customer’s satisfaction.
- Product Knowledge:Knowledge about the company’s products or services is essential for delivering good customer service. Customer service representatives should be well-informed about the features, benefits, and uses of the products or services they support, enabling them to answer customer questions accurately and provide helpful guidance.
- Adaptability:Customer service representatives should be adaptable and flexible, able to adjust their approach to meet the unique needs and preferences of each customer. They should be willing to accommodate changes, handle unexpected situations, and tailor their responses accordingly to ensure a positive customer experience.
- Positive Attitude:Maintaining a positive attitude is vital in customer service. Good customer service representatives greet customers warmly, express enthusiasm, and project a friendly and approachable demeanor. They strive to create a positive atmosphere and leave customers feeling valued and satisfied with their interaction.
By embodying these qualities, customer service representatives can effectively meet customer needs, build trust and loyalty, and contribute to the overall success of the business.
FAQs
What are Ultrathin Antenna PCBs?
Ultrathin Antenna PCBs are printed circuit boards that are specifically designed to function as antennas for wireless communication devices. They are characterized by their thin and flexible nature, making them suitable for integration into small and compact electronic devices.
What are the advantages of Ultrathin Antenna PCBs?
Ultrathin Antenna PCBs offer several advantages, including compact size, low profile, flexibility, durability, customization options, and compatibility with modern electronic devices.
What materials are used in Ultrathin Antenna PCBs?
Common substrate materials for Ultrathin Antenna PCBs include polyimide (PI), liquid crystal polymer (LCP), and polyester (PET). These materials provide mechanical flexibility while maintaining electrical performance.
What are some typical applications of Ultrathin Antenna PCBs?
Ultrathin Antenna PCBs are used in various wireless communication applications, including smartphones, tablets, wearables, Internet of Things (IoT) devices, smart home devices, automotive electronics, medical devices, and more.
How are Ultrathin Antenna PCBs manufactured?
The manufacturing process for Ultrathin Antenna PCBs involves substrate preparation, antenna pattern formation using techniques like photolithography or printing, metallization, etching, surface finishing, assembly, testing, and packaging.
What factors should be considered when designing Ultrathin Antenna PCBs?
Important design considerations include substrate selection, antenna geometry, ground plane design, trace width and spacing, feedline design, antenna placement, radiation pattern optimization, flexibility considerations, and manufacturability.
What are the key specifications to look for in Ultrathin Antenna PCBs?
Key specifications include frequency bands supported, impedance matching, radiation efficiency, gain, polarization, dimensions, flexibility, and environmental considerations such as temperature range and moisture resistance.