Ultrathin Rogers PCB Manufacturer
Ultrathin Rogers PCB Manufacturer,Ultrathin Rogers PCB is a high-performance printed circuit board made from ultra-thin materials, designed for high-frequency and high-speed applications. It offers excellent dielectric properties and thermal conductivity, ensuring stable signal transmission in extremely thin laminates. This PCB is widely used in RF, microwave, and communication devices, supporting high-density circuit layouts and miniaturization. Ultrathin Rogers PCB excels in enhancing device performance and reducing signal loss, making it an ideal choice for various complex electronic applications, providing reliable solutions in high-frequency domains.
What is an Ultrathin Rogers PCB?
An Ultrathin Rogers PCB refers to a type of printed circuit board (PCB) that utilizes Rogers Corporation’s high-performance materials in an extremely thin form factor. Rogers PCBs are known for their excellent electrical properties, including low dielectric loss, high-frequency performance, and thermal stability.
Ultrathin Rogers PCBs are specifically designed to be thinner than standard PCBs, typically less than 0.2mm in thickness. This ultra-thin profile is advantageous in applications where space constraints are critical, such as in mobile devices, aerospace systems, and high-speed communication equipment.
The use of Rogers materials in these PCBs ensures that they can handle high frequencies without significant signal loss, making them ideal for applications requiring high-speed data transmission and signal integrity. Their thermal stability also allows them to operate reliably in environments with varying temperatures.
Manufacturing Ultrathin Rogers PCBs requires precise handling and processing techniques due to their thinness and the sensitivity of Rogers materials. Specialized equipment and expertise are necessary to ensure the PCBs meet stringent performance requirements and reliability standards demanded by modern electronic applications.
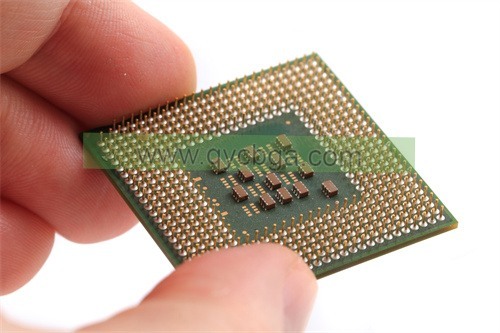
Ultrathin Rogers PCB Manufacturer
What are the Ultrathin Rogers PCB Design Guidelines?
Designing Ultrathin Rogers PCBs requires careful consideration of several key guidelines to ensure optimal performance and reliability:
- Material Selection: Choose appropriate Rogers high-frequency laminates that are specifically designed for ultrathin applications. These materials should offer low dielectric constant (Dk) and low dissipation factor (Df) to minimize signal loss at high frequencies.
- Layer Stackup: Optimize the layer stackup to maintain signal integrity and mechanical stability while keeping the overall thickness minimal. Consider using thinner copper layers and reducing the number of layers if possible to meet size and weight constraints.
- Routing and Trace Geometry: Use controlled impedance routing techniques to match signal integrity requirements. Maintain consistent trace widths and spacing to minimize signal losses and electromagnetic interference (EMI). Avoid sharp corners and use appropriate via designs to maintain signal integrity.
- Thermal Management: Despite their thin profile, ensure adequate thermal management to prevent overheating. Design for efficient heat dissipation through the use of thermal vias, copper pours, and strategic component placement.
- Mechanical Considerations: Ultrathin PCBs are more susceptible to mechanical stress and flexing. Reinforce the board with additional support structures or stiffeners if needed, especially in applications subject to vibration or mechanical shock.
- Manufacturing Constraints: Consider the capabilities of PCB manufacturers in handling ultrathin materials and precise tolerances. Specify clear manufacturing tolerances and requirements to ensure consistent production quality.
- Testing and Validation: Perform rigorous testing and validation of prototypes to verify electrical performance, signal integrity, and reliability under expected operating conditions. Use simulation tools to predict and optimize PCB performance before fabrication.
By following these design guidelines, engineers can effectively harness the benefits of Ultrathin Rogers PCBs, ensuring they meet stringent performance requirements for high-frequency applications while maintaining reliability and manufacturability.
What is the Ultrathin Rogers PCB Fabrication Process?
The fabrication process for Ultrathin Rogers PCBs involves several specialized steps to ensure the board meets high-frequency performance requirements while maintaining its thin profile. Here are the key steps typically involved in the fabrication process:
- Material Selection:Choose Rogers high-frequency laminate materials specifically designed for ultrathin PCB applications. These materials typically have low dielectric constant (Dk) and low dissipation factor (Df) to minimize signal loss at high frequencies.
- Preparation of Substrate: Begin by preparing the substrate material to the desired thickness. This may involve laminating thin layers of Rogers laminate together to achieve the required overall thickness.
- Panelization: Arrange individual PCB designs on a panel for efficient fabrication. Panelization helps optimize material usage and enhances manufacturing efficiency.
- Drilling: Precision drilling is performed to create holes for vias and component mounting pads. Ultrathin PCBs require careful handling during drilling to prevent damage to the delicate substrate.
- Copper Cladding: Apply thin layers of copper to the substrate using processes such as electroplating or lamination. The copper layers are patterned to form circuit traces and pads using photolithography and etching techniques.
- Layer Alignment and Lamination: If the PCB design requires multiple layers, align and laminate the layers together using heat and pressure. This step ensures proper registration of conductive layers and dielectric materials.
- Etching and Plating: Use chemical etching to remove unwanted copper from the substrate, leaving behind the desired circuit patterns. Copper plating may be used to enhance trace thickness and conductivity.
- Surface Finish: Apply a surface finish to protect exposed copper and facilitate soldering of components. Common surface finishes include immersion gold, HASL (Hot Air Solder Leveling), and OSP (Organic Solderability Preservatives).
- Solder Mask Application: Apply solder mask over the PCB surface, leaving exposed only the areas where components will be soldered. Solder mask helps protect the PCB from environmental factors and prevents solder bridges.
- Silkscreen Printing: Optionally, silkscreen printing is used to apply component identifiers, logos, and other markings on the PCB surface.
- Quality Assurance:Conduct thorough quality checks and inspections throughout the fabrication process to ensure dimensional accuracy, electrical continuity, and adherence to design specifications.
- Testing: Perform electrical testing to verify the functionality and performance of the finished PCB. This may include checks for impedance, continuity, insulation resistance, and signal integrity.
- Final Inspection and Packaging: After testing, inspect the PCBs for any defects or issues. Once approved, the PCBs are cleaned, packaged, and prepared for shipment or assembly.
The fabrication of Ultrathin Rogers PCBs requires specialized equipment and expertise to handle the delicate materials and precise tolerances involved. Manufacturers with experience in high-frequency PCB fabrication and Rogers materials are essential to ensure the boards meet stringent performance requirements for demanding applications.
How do you Manufacture an Ultrathin Rogers PCB?
Manufacturing an Ultrathin Rogers PCB involves a series of specialized steps and considerations to ensure high-frequency performance and reliability in a thin form factor:
- Material Selection: Choose Rogers high-frequency laminates designed for ultrathin PCBs, typically with low Dk and Df characteristics to minimize signal loss at high frequencies.
- Substrate Preparation: Begin by preparing the Rogers laminate to achieve the desired thinness. This may involve laminating thin layers of Rogers material to achieve the overall thickness required for the PCB.
- Panelization: Arrange individual PCB designs on a panel layout to optimize material usage and facilitate efficient fabrication processes.
- Drilling: Precisely drill holes for vias and component mounting pads. Careful handling during drilling is crucial to avoid damaging the thin and delicate Rogers substrate.
- Copper Deposition: Apply thin layers of copper to the substrate through processes like electroplating or lamination. These copper layers form the conductive traces and pads on the PCB.
- Layer Alignment and Lamination: If multiple layers are required, align and laminate them together using heat and pressure. This ensures proper registration of conductive layers and dielectric materials.
- Etching and Plating:Use chemical etching to remove excess copper and define the circuit patterns on the PCB. Additional copper plating may be applied to enhance trace thickness and conductivity.
- Surface Finish Application: Apply a suitable surface finish to protect exposed copper and facilitate soldering. Common finishes include immersion gold, HASL (Hot Air Solder Leveling), and OSP (Organic Solderability Preservatives).
- Solder Mask Application: Apply solder mask over the PCB surface, leaving openings for component pads. Solder mask protects the PCB from environmental factors and prevents solder bridges during assembly.
- Silkscreen Printing: Optionally, apply silkscreen markings for component identifiers, logos, and other required information on the PCB surface.
- Quality Control: Conduct rigorous inspections and tests throughout the manufacturing process to ensure dimensional accuracy, electrical continuity, and adherence to design specifications.
- Electrical Testing: Perform comprehensive electrical tests to verify the functionality and performance of the PCB, including impedance testing and signal integrity analysis.
- Final Inspection and Packaging: Inspect the finished PCBs for any defects or issues. Clean and carefully package the PCBs for shipment or assembly.
Manufacturing Ultrathin Rogers PCBs requires specialized equipment and expertise due to the delicate nature of Rogers materials and the precision needed for high-frequency applications. Working with experienced PCB manufacturers familiar with Rogers laminates and high-frequency design principles is crucial to ensure the PCBs meet stringent performance requirements and reliability standards.
How Much Should an Ultrathin Rogers PCB Cost?
The cost of Ultrathin Rogers PCBs can vary widely depending on several factors:
- Board Size and Complexity: Larger and more complex PCBs require more materials and longer manufacturing times, which can increase costs.
- Number of Layers: Ultrathin PCBs can be single-layer or multi-layered. Multi-layered PCBs typically cost more due to additional material and processing requirements.
- Material Type and Thickness: Rogers high-frequency materials are generally more expensive than standard PCB materials due to their advanced properties. Ultrathin versions of these materials may incur additional costs.
- Surface Finish and Coating: Different surface finishes such as immersion gold or OSP can affect costs. Some finishes, especially those optimized for high frequencies, may add to the overall cost.
- Manufacturing Process: Specialized processes such as controlled impedance routing and precise drilling required for Ultrathin PCBs can impact costs.
- Quantity:Larger production quantities often result in lower per-unit costs due to economies of scale. However, prototype or small-batch orders may have higher costs per unit.
- Lead Time:Expedited production schedules or quick-turn services may come at an additional cost.
As a rough estimate, Ultrathin Rogers PCBs can range from several dollars to tens of dollars per square inch, depending on the above factors. For a more accurate cost estimate, it’s advisable to consult with PCB manufacturers who specialize in Rogers materials and can provide quotes based on specific design requirements and production volumes. Getting multiple quotes and comparing services and capabilities can help in finding the best balance between cost, quality, and lead time for Ultrathin Rogers PCB fabrication.
What is Ultrathin Rogers PCB Base Material?
The base material used for Ultrathin Rogers PCBs typically consists of specialized high-frequency laminates produced by Rogers Corporation. These laminates are engineered to provide excellent electrical performance, thermal stability, and mechanical integrity in a thin form factor. Some key characteristics of the base material include:
- Low Dielectric Constant (Dk):Ultrathin Rogers PCB base materials are designed to have a low Dk, which helps in minimizing signal loss at high frequencies. This property is crucial for maintaining signal integrity in high-speed communication and RF applications.
- Low Dissipation Factor (Df): The base materials also have a low Df, ensuring efficient transmission of signals without significant energy loss due to heat dissipation.
- Thin Profile: As the name suggests, the base materials are manufactured to be ultrathin, typically less than 0.2mm in thickness. This thin profile is advantageous in applications where space and weight constraints are critical.
- High Thermal Conductivity: Despite their thinness, Ultrathin Rogers PCB base materials often feature high thermal conductivity, allowing efficient dissipation of heat generated during operation. This property helps in maintaining the reliability and longevity of electronic components.
- Mechanical Strength: Although thin, these materials are engineered to provide adequate mechanical strength and dimensional stability to withstand the rigors of PCB fabrication processes and environmental conditions.
- Compatibility with High-Frequency Design: The base materials are tailored to support high-frequency designs, ensuring consistent performance across a wide range of frequencies.
Examples of specific Rogers high-frequency laminates used for Ultrathin Rogers PCBs include materials from the RO3000® and RO4000® series. These materials are widely recognized in the industry for their performance in demanding RF and microwave applications where precise signal integrity and reliability are essential.
Which Company Makes Ultrathin Rogers PCB?
Ultrathin Rogers PCBs are typically manufactured by specialized PCB manufacturing companies that possess advanced technology and extensive experience in handling high-frequency materials and precise manufacturing processes. In this field, several globally renowned PCB manufacturers and suppliers can produce and supply Ultrathin Rogers PCBs to meet various needs in high-frequency and microwave applications.
Rogers Corporation itself is a major manufacturer of high-frequency materials, offering various series of Rogers high-frequency laminates, including products suitable for Ultrathin PCBs. However, the actual production of PCBs is often carried out by specialized PCB manufacturers who have the capability to work with these high-performance materials.
For our company, we also offer services in the manufacturing and supply of Ultrathin Rogers PCBs. As an experienced PCB manufacturer, we have the following strengths and capabilities:
- Professional Design and Engineering Team: We have a professional PCB design and engineering team capable of customizing designs and optimizing them according to the requirements of high-frequency applications.
- Advanced Manufacturing Equipment: We have invested in and possess advanced manufacturing equipment and technology capable of handling high-frequency materials such as Rogers high-frequency laminates, ensuring the production of high-quality Ultrathin Rogers PCBs.
- Strict Quality Control: We implement a rigorous quality management system, conducting strict quality control and inspection at every stage from raw material procurement to production, ensuring that each product meets design specifications and customer requirements.
- Flexible Production Capacity: We have flexible production capabilities to meet the needs ranging from prototypes to large-scale production, promptly responding to customer orders.
- Customer Service and Technical Support: We prioritize customer service and technical support, providing comprehensive pre-sales consultation and after-sales service to ensure customer satisfaction and effective solutions throughout the project cycle.
In summary, our company not only has the capability to manufacture and supply Ultrathin Rogers PCBs but also offers customized solutions through professional expertise and services to meet various needs in high-frequency and microwave applications. We are committed to delivering high-quality, reliable PCB products that support our customers’ success in their respective fields.
What are the 7 Qualities of Good Customer Service?
The 7 qualities of good customer service are:
- Responsiveness: Being prompt and timely in addressing customer inquiries, requests, and issues. This includes acknowledging customers promptly and providing timely updates or resolutions.
- Empathy:Understanding and empathizing with the customer’s situation or problem. This involves actively listening to their concerns, showing compassion, and demonstrating a genuine desire to help.
- Clear Communication: Communicating clearly and effectively with customers. This includes using simple language, explaining complex issues in understandable terms, and ensuring that information is conveyed accurately.
- Knowledgeability: Possessing adequate product knowledge and expertise to answer customer questions and provide solutions. Customers value dealing with knowledgeable representatives who can offer accurate information and advice.
- Professionalism: Maintaining a professional demeanor and attitude in all customer interactions. This includes being courteous, respectful, and maintaining composure even in challenging situations.
- Problem-Solving Skills: Having strong problem-solving abilities to resolve customer issues effectively. This involves identifying root causes, exploring alternative solutions, and taking proactive steps to address concerns.
- Personalization: Providing personalized service that meets the individual needs and preferences of each customer. This may involve remembering customer preferences, addressing them by name, and tailoring solutions to their specific situation.
These qualities collectively contribute to a positive customer service experience, fostering customer satisfaction, loyalty, and positive word-of-mouth recommendations. Businesses that prioritize these qualities often build strong relationships with their customers and differentiate themselves in competitive markets.
FAQs
What is an Ultrathin Rogers PCB?
An Ultrathin Rogers PCB is a printed circuit board that uses Rogers Corporation’s high-frequency laminates in an extremely thin form factor, typically less than 0.2mm thick. These PCBs are designed for high-frequency and microwave applications where space and weight constraints are critical.
What are the advantages of Ultrathin Rogers PCBs?
Advantages include excellent high-frequency performance with low dielectric constant (Dk) and low dissipation factor (Df), minimal signal loss, high thermal stability, and mechanical integrity in a thin profile. They are suitable for applications requiring reliable signal transmission and thermal management in compact electronic devices.
Where are Ultrathin Rogers PCBs used?
They are used in various high-frequency applications such as telecommunications, aerospace and defense systems, radar systems, satellite communications, medical devices, and automotive radar systems. These applications benefit from the PCBs’ ability to handle high frequencies without significant signal loss.
How are Ultrathin Rogers PCBs manufactured?
Ultrathin Rogers PCBs are manufactured using specialized processes that involve precise handling of Rogers high-frequency laminates. Steps include material preparation, layer stackup design, precise drilling, copper deposition and etching, surface finishing, solder mask application, and thorough quality control measures to ensure performance and reliability.
What factors affect the cost of Ultrathin Rogers PCBs?
Cost factors include the size and complexity of the PCB design, number of layers, type and thickness of Rogers laminate used, surface finish options, manufacturing processes involved (such as controlled impedance routing), quantity ordered, and lead time requirements.
Are Ultrathin Rogers PCBs more difficult to manufacture compared to standard PCBs?
Yes, Ultrathin Rogers PCBs can be more challenging to manufacture due to their thin profile and the advanced properties of Rogers high-frequency materials. Specialized equipment and expertise are required to ensure precise handling and processing of these materials while maintaining high-quality standards.
What should I consider when designing an Ultrathin Rogers PCB?
Considerations include selecting the appropriate Rogers laminate for your frequency requirements, optimizing the layer stackup for signal integrity, employing controlled impedance routing techniques, ensuring adequate thermal management, and verifying design feasibility with a trusted PCB manufacturer experienced in high-frequency applications.